In order to improve the quality of the finished product, some manufacturers have purchased underwater pelletizer, but found that the moisture content of the pellets still cannot come down.
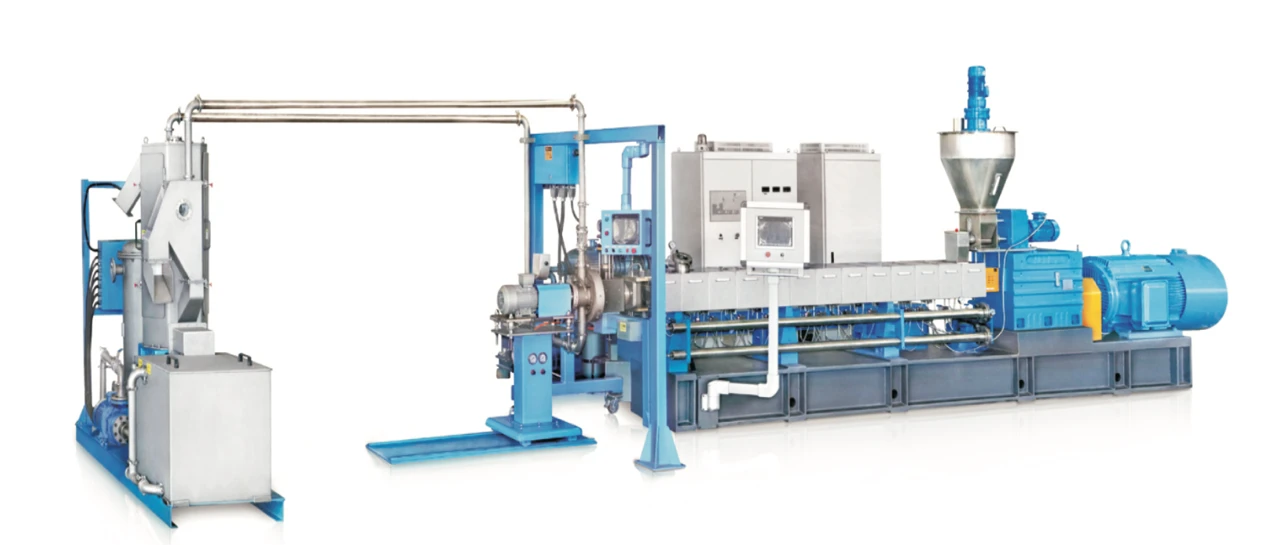
In the production of plastic pellets, the cutting systems are mainly cold strand cutting, hot air die face cutting, water ring cutting, and underwater cutting. The cutting method affects the water on the surface of the plastic pellets, and the water content directly affects the quality of the finished pellets. Among these cutting methods, the water content of the underwater cutting method is relatively difficult to control.
So what are the factors that affect the water content of the finished pellets from underwater pelletizer?
Cutting blade in the application process will occur wear, when the blade wear to a certain extent, cutting pellets will take some burrs, these burrs adsorbed water in the subsequent drying process is difficult to remove, resulting in high water content.
When the material comes out from the mold, the instant pressure release swells up, and the water is easily wrapped in the material and vaporized to form a hole, and the water contained in the material cannot be discharged through subsequent drying.
Too small mold pressure makes the material extruded from the mold less dense, and the water infiltrates into the granule during the granule transfer process. The infiltrated water is difficult to take out in the dewatering process.
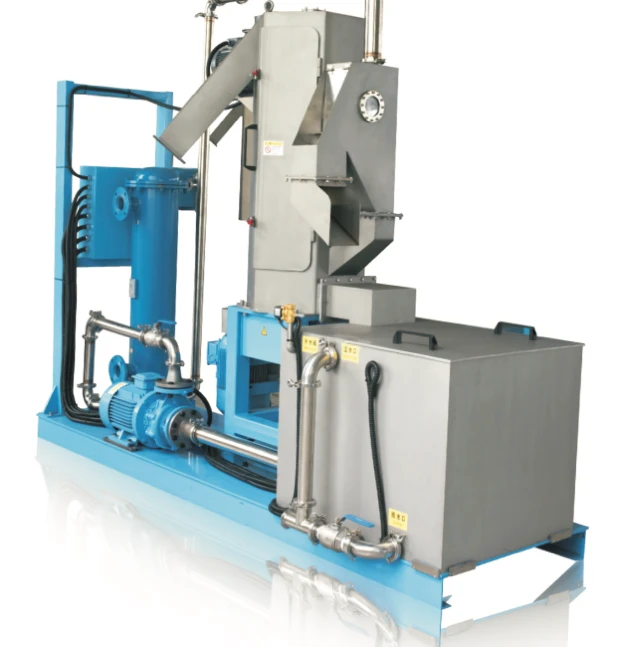
As we all know, the efficiency of hot water dewatering is relatively higher than that of cold water, and even if we use the cold strand-cutting method, the most effective way to dewater is to blow hot air. That is why the water content of the pellets is high when the machine is just turned on, because when the machine is turned on, the water in the tank enters the circulation system is too low, the temperature has to be reduced, and then the heat brought out from the pelletizer by the pellets to raise the temperature.
Will someone say: that you can first raise the water tank’s temperature so that the problem will be solved? To be honest, the water tank is slow to heat up, and even slower to cool down, I have tried, our pelletizer water tank to reduce the temperature of 1 ℃ takes about 7 minutes or so. Of course, feeding cold water into the tank to cool down fast, but sometimes it is impossible to feed cold water.
The tank water temperature is too low not only affects the dewatering efficiency in the dewatering machine, and because the water temperature is too low, it will affect the mold temperature, which brings the result that the head pressure is too high.
If the water tank temperature too low is not good, then the water tank temperature high is good? The real practice has proved that a water tank temperature too high is not good, too high-water tank temperature lets the particle cooling speed lower, easy to form craters on the surface of the pellets, at the same time, too high water temperature will bring the expansion of the pellets, with the gradual cooling of the pellet contraction, the water remains in the material.
If the water tank temperature too low is not good, then the water tank temperature high is good? The real practice has proved that a water tank temperature too high is not good, too high-water tank temperature lets the particle cooling speed lower, easy to form craters on the surface of the pellets, at the same time, too high water temperature will bring the expansion of the pellets, with the gradual cooling of the pellet contraction, the water remains in the material.
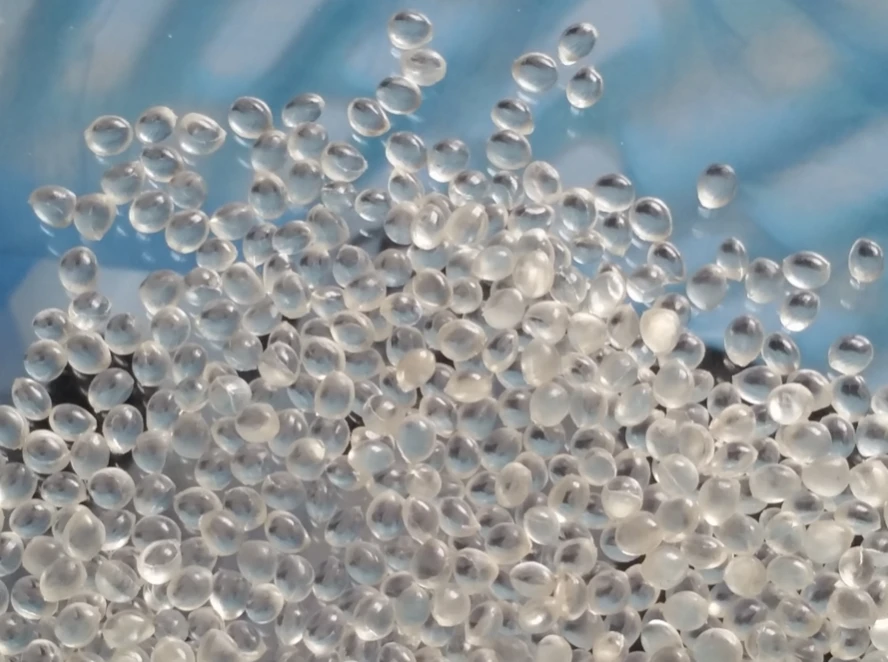
Content source: Internet; Liansu.com; organized by Xinda
Disclaimer: (Part of) the data, charts or other content in this article comes from the Internet or other publicly published materials, and is for readers’ reference, communication, and learning only, and does not involve any commercial behavior or purpose. The copyright belongs to the original author and original source. If the copyright owner believes that this article is suspected of infringement or other problems, please contact us and deal with it in time.