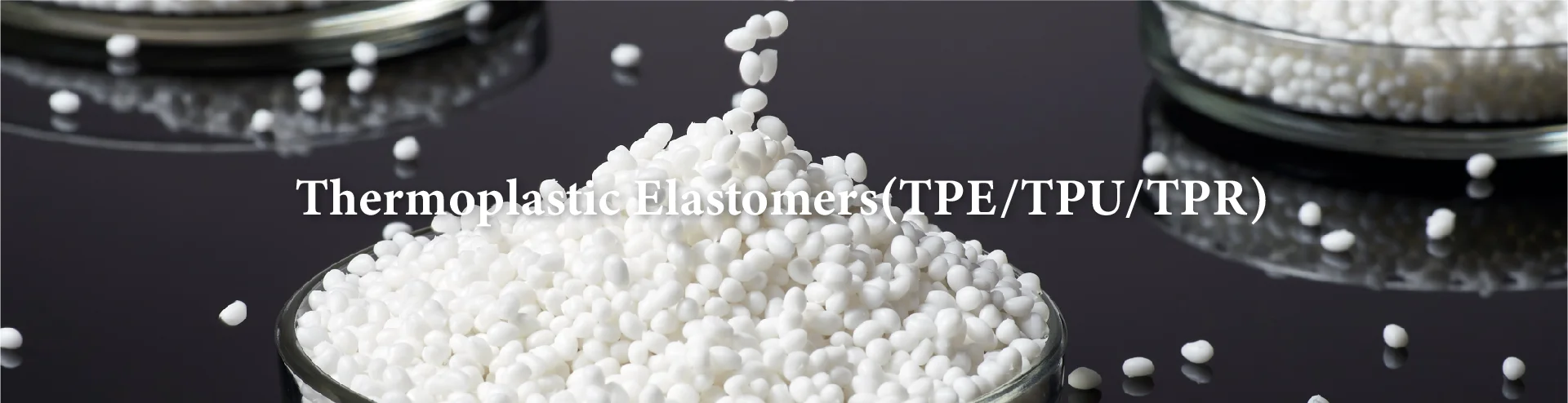
Compounding technology for Thermoplastic Elastomer(TPE/TPU/TPR)
Compounding technology for thermoplastic elastomers (TPEs), thermoplastic polyurethane (TPU), and thermoplastic rubber (TPR) involves a similar process to rubber compounding. But thermoplastic elastomer compounds have some important differences.

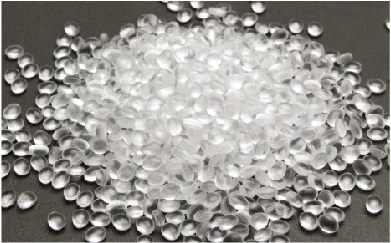
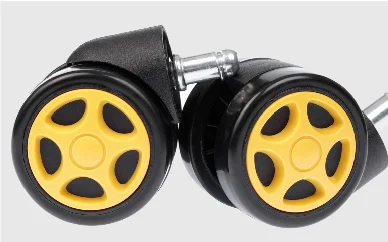
The process typically involves the following steps:
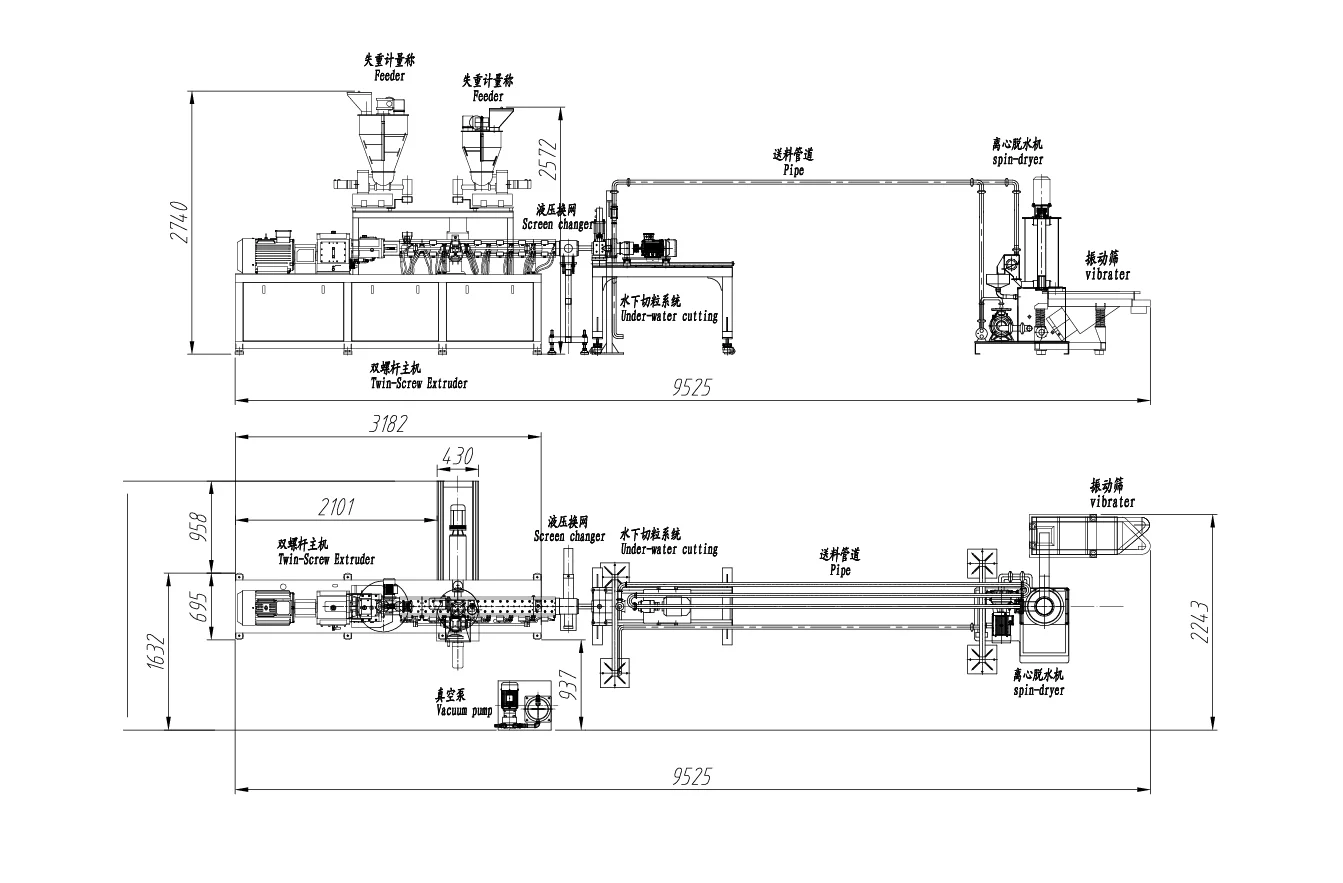
Mixing:
The raw materials, including the polymer, fillers, plasticizers, and other additives, are combined in a mixing chamber, such as a twin-screw extruder, and mixed together until they are evenly distributed.
Melt processing:
The mixture is then subjected to heat and pressure, which melts the polymer and activates any curing agents or cross-linking agents.
Cooling and solidification:
The melted mixture is then cooled and solidified to form a solid elastomeric material.
Testing:
The final product is then tested to ensure that it meets the desired specifications for properties such as hardness, tensile strength, elongation, and resilience.
>>
There are several factors that must be considered when compounding TPEs, TPU, and TPR, including the specific properties required for the final product, the processing conditions, and the cost and availability of raw materials. Fillers, plasticizers, and other additives may be added to improve properties such as flexibility, durability, and heat resistance.
Unlike rubber compounds, TPEs, TPU, and TPR are thermoplastic materials, meaning they can be melted and re-molded multiple times without losing their elastomeric properties. This makes them highly versatile and easy to process, allowing for greater flexibility in design and manufacturing.
Overall, the compounding technology for TPEs, TPU, and TPR is a complex and specialized process that requires a deep understanding of the properties of the materials involved and the desired end-use applications.

Xinda Co Kneader
thermoplastic(TPE/TPU/TPR) compounding systems offer several specific benefits
> Improved mixing:
The co-kneader design allows for better dispersion of raw materials, resulting in a more homogeneous mixture and improved quality of the final product.
> Reduced energy consumption:
The co-kneader design reduces energy consumption during the mixing process, resulting in lower operating costs.
> Higher productivity:
The co-kneader design allows for faster mixing and shorter cycle times, resulting in higher productivity and reduced manufacturing costs.
> Easy maintenance:
The co-kneader design is easy to clean and maintain, resulting in reduced downtime and improved efficiency.
> Greater flexibility:
The co-kneader design can handle a wide range of raw materials, including high-viscosity and low-viscosity materials, as well as materials with varying melt temperatures, making it a highly versatile tool for compounding.
> Overall:
The XINDA Co-kneader thermoplastic compounding system offers a number of advantages over traditional thermoplastic compounding systems, making it a highly attractive option for manufacturers in the TPE/TPU/TPR compounding industry.
> Precise control of temperature and pressure:
The co-kneader design provides precise control of temperature and pressure, allowing for greater consistency in the manufacturing process and improved product quality.
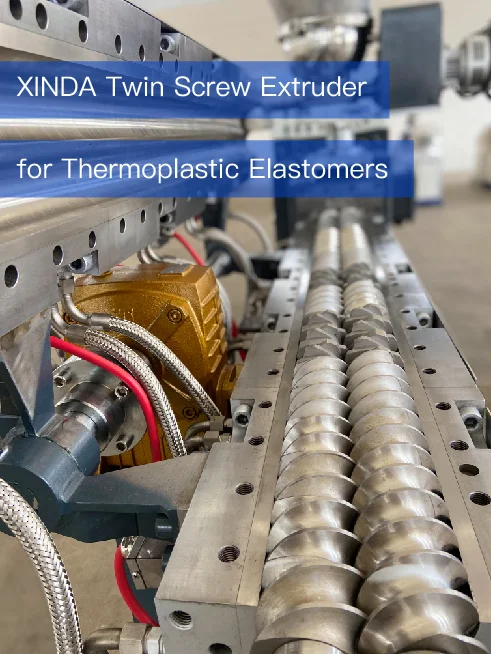
Why Xinda’s Twin Screw Extruder different?
> Clamshell Barrel:
Clamshell Barrel: The barrel can be quickly opened for cleaning and maintenance. According to material variety and different technological requirements,it can be flexible combined into an ideal structure to improve the overall utilization rate of the equipment.