
about the extruder
Semi-conductive Cable Compounds
Semi-conductive cable compounds are used in the wire and cable industry as two semi-conductive layers for enclosing crosslinked Polyethylene (XLPE) layers to ensure the insulation performance of medium- and high-voltage power cables. The production process requires that the conductive carbon black structure is not destroyed, highly dispersed into a polymer matrix, and evenly distributed to the melts to obtain a homogeneous compound. At the same time, the polymer is required to be degraded as little as possible.
Product Quality Index
Energy Generation
Processing Steps:
Material handling system-Compounding and extrusion- Wate ring pelletizer -Spin dryer – Classify – Packing system
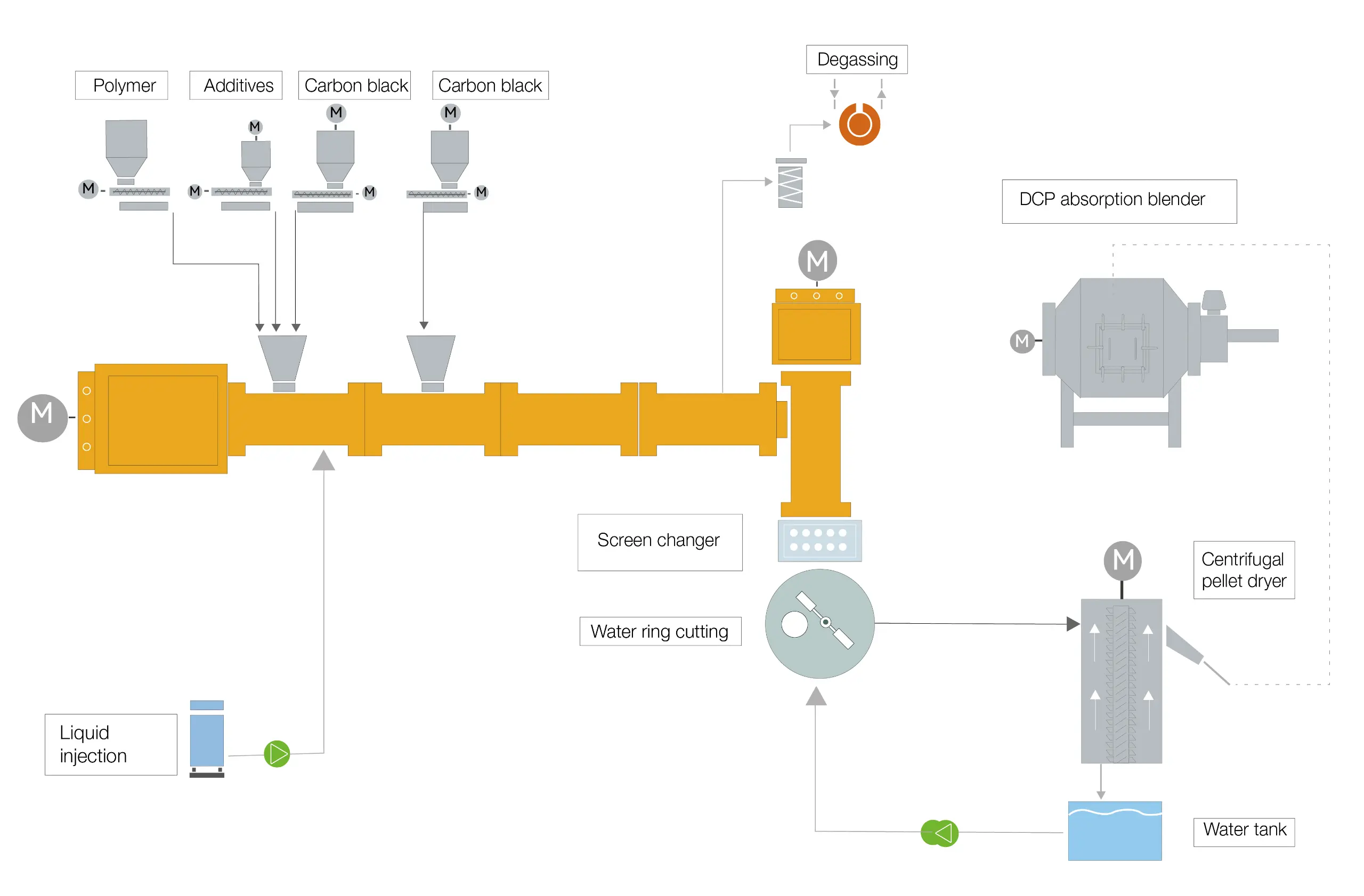
Xinda in Cable Compounding Industry
Xinda Co-Kneader is used by well-known cable companies worldwide, specializing in the production of PVC, HFFR, XLPE, PEX cross-linkable and semi-conductive cable compounds.
Gentle Shearing
Low Process Temperature
Precise temperature control
Flexible Screw Configurations
High Filling Rate of Inorganic Powder
Uniform Distribution of Various Additives
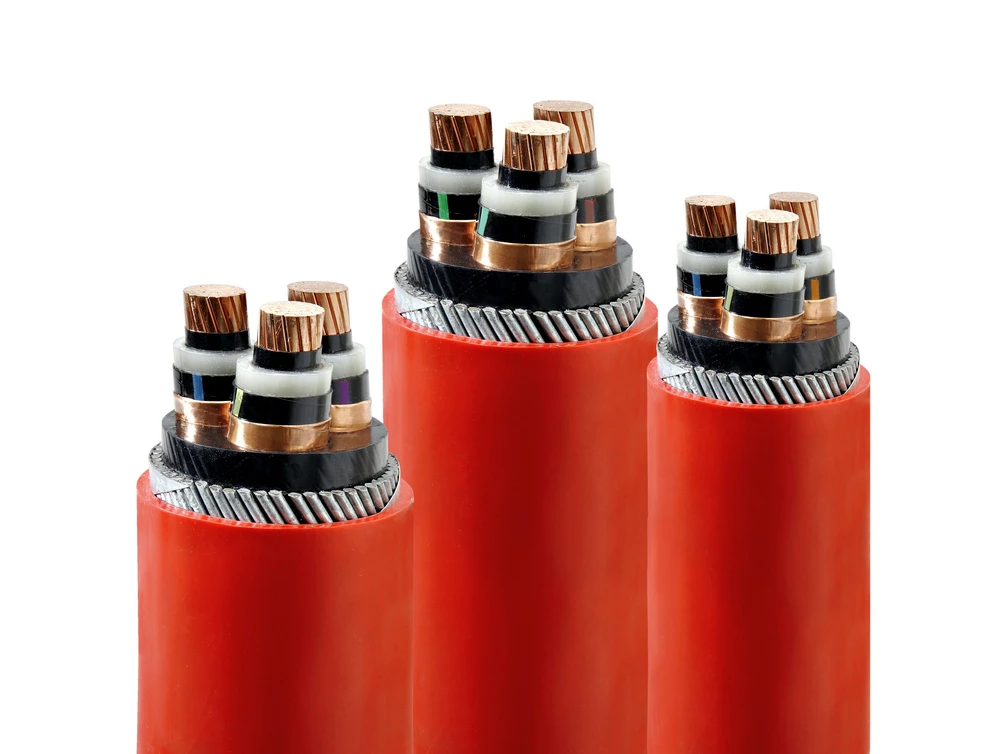
Working Principle

Classic Single Screw
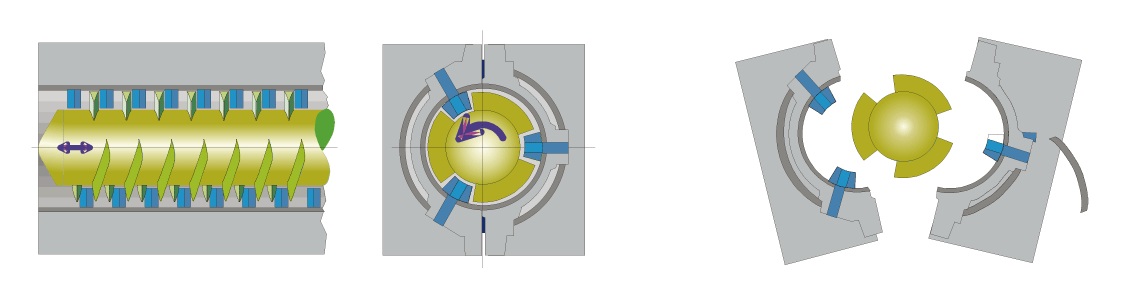
Co Kneader
Liquid Injection System
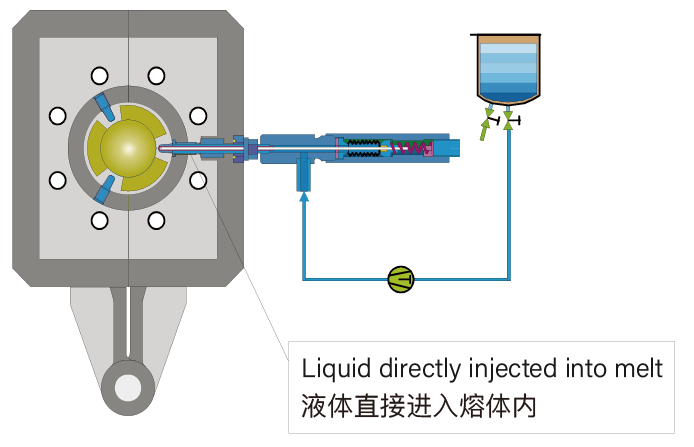
The liquids are directly injected into the melt at the appropriate time and place
The process is extremely accurate, safe and hazard free
There are no losses due to volatilisation and no deposits on metal surface
Shear Mechanism in the Co-Kneader
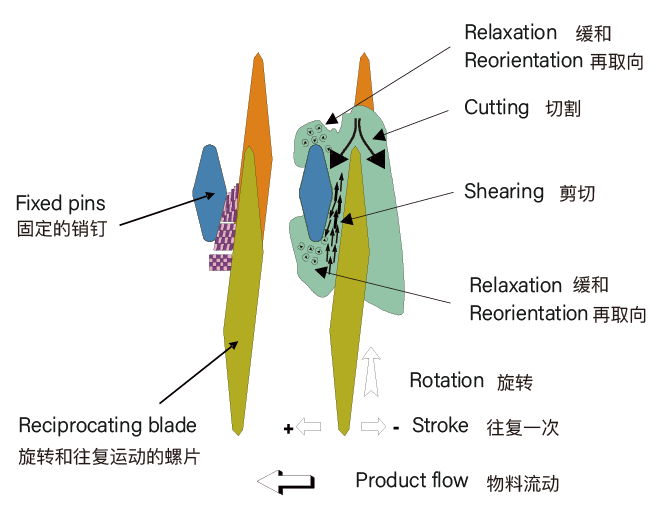
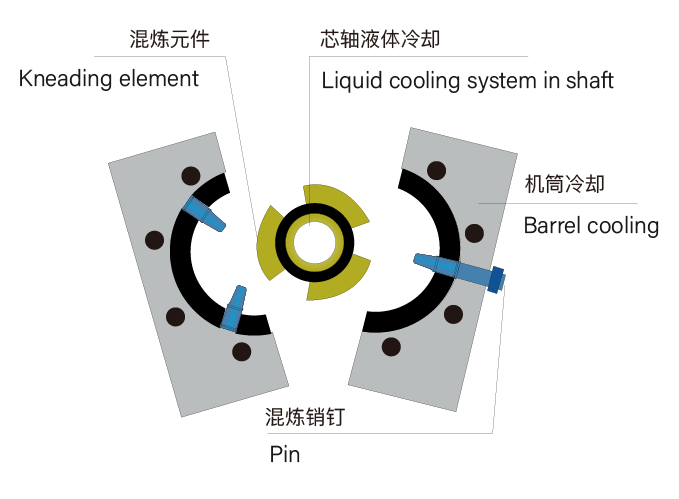
Hollow Pins for Thermocouple
Direct immersion in polymer
Precise melt temperature
Temperature stability of the process
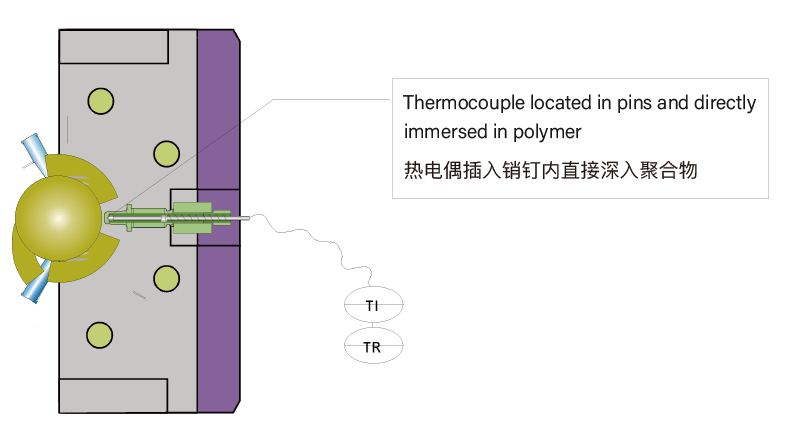
Temperature Control
Barrel: Liquid or electrically heated / Water Cooled
Shaft: Liquid heated/ cooled
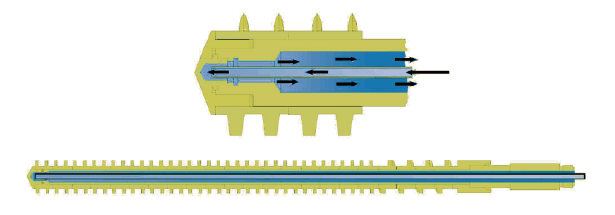
Easy adaptation of screw configuration
The screw consists of individual elements, that can easily be exchanged or replaced
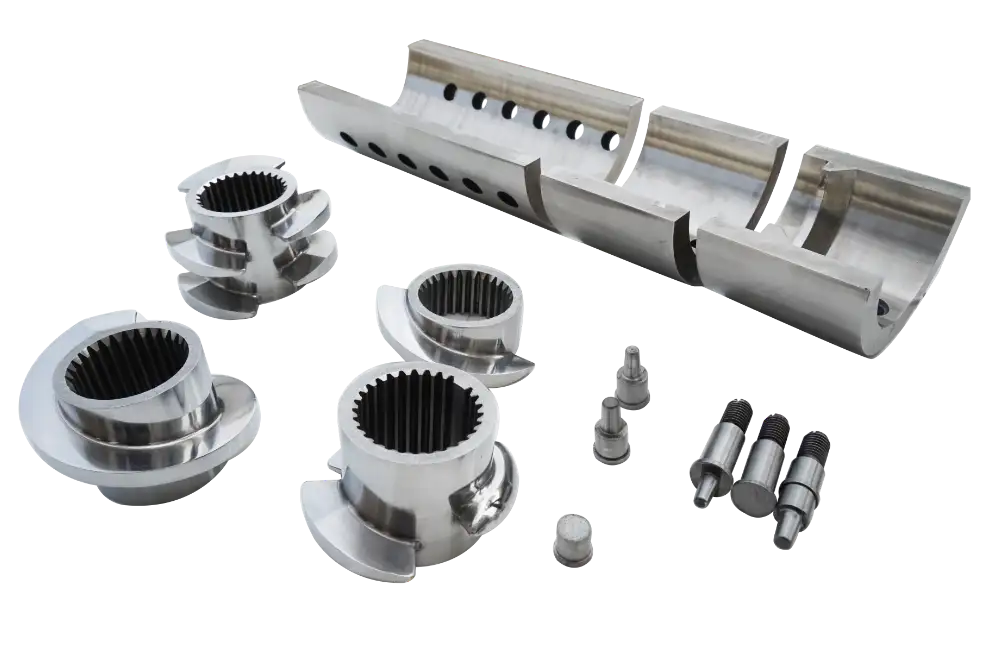
-恢复的.webp)
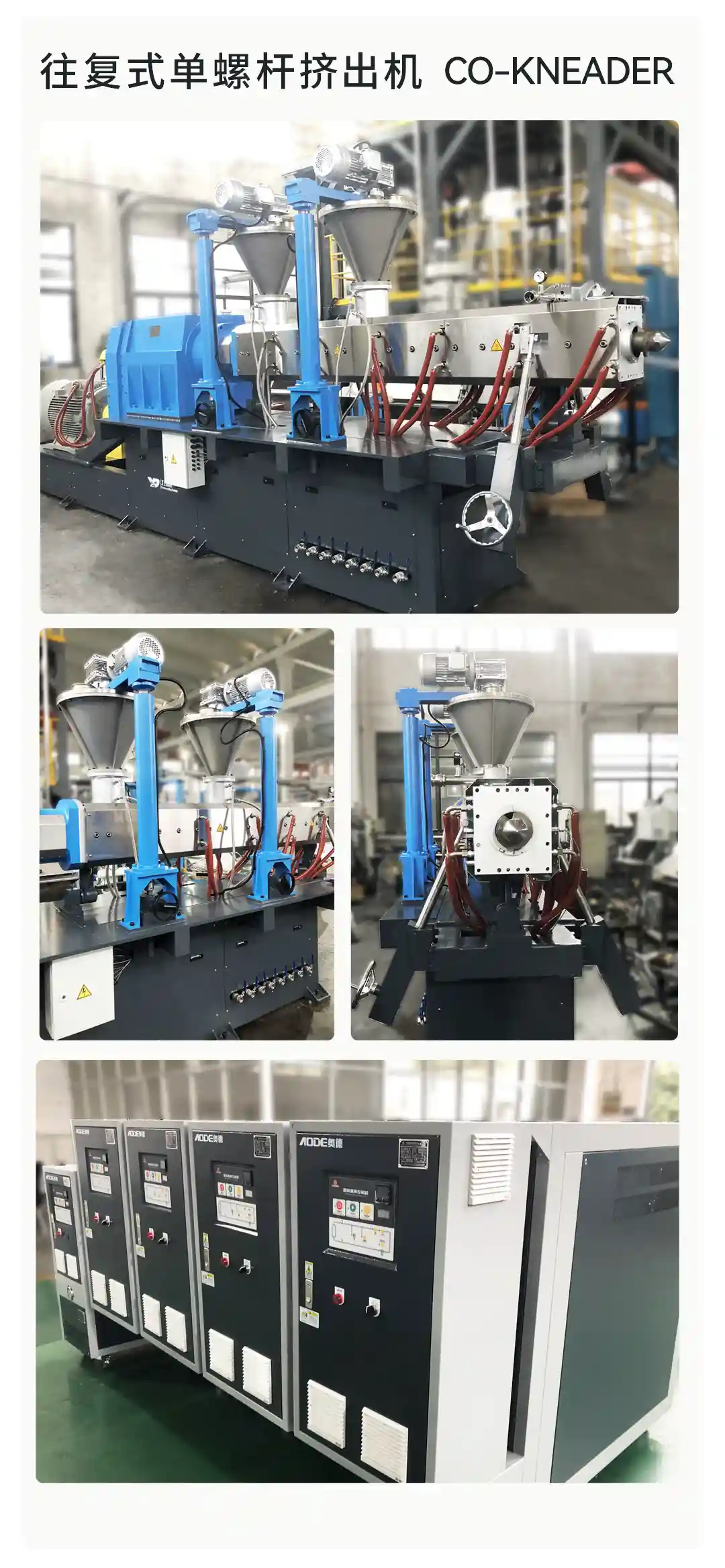
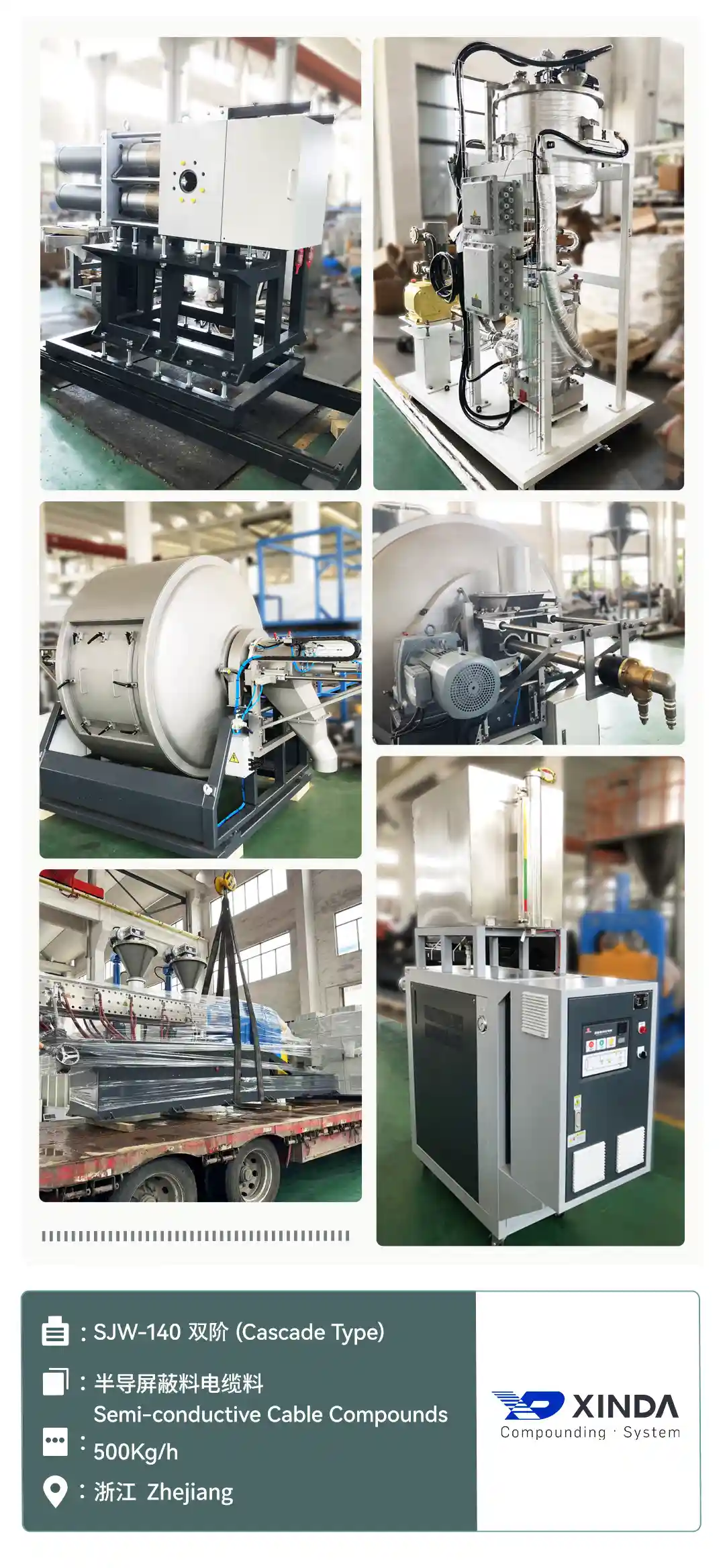
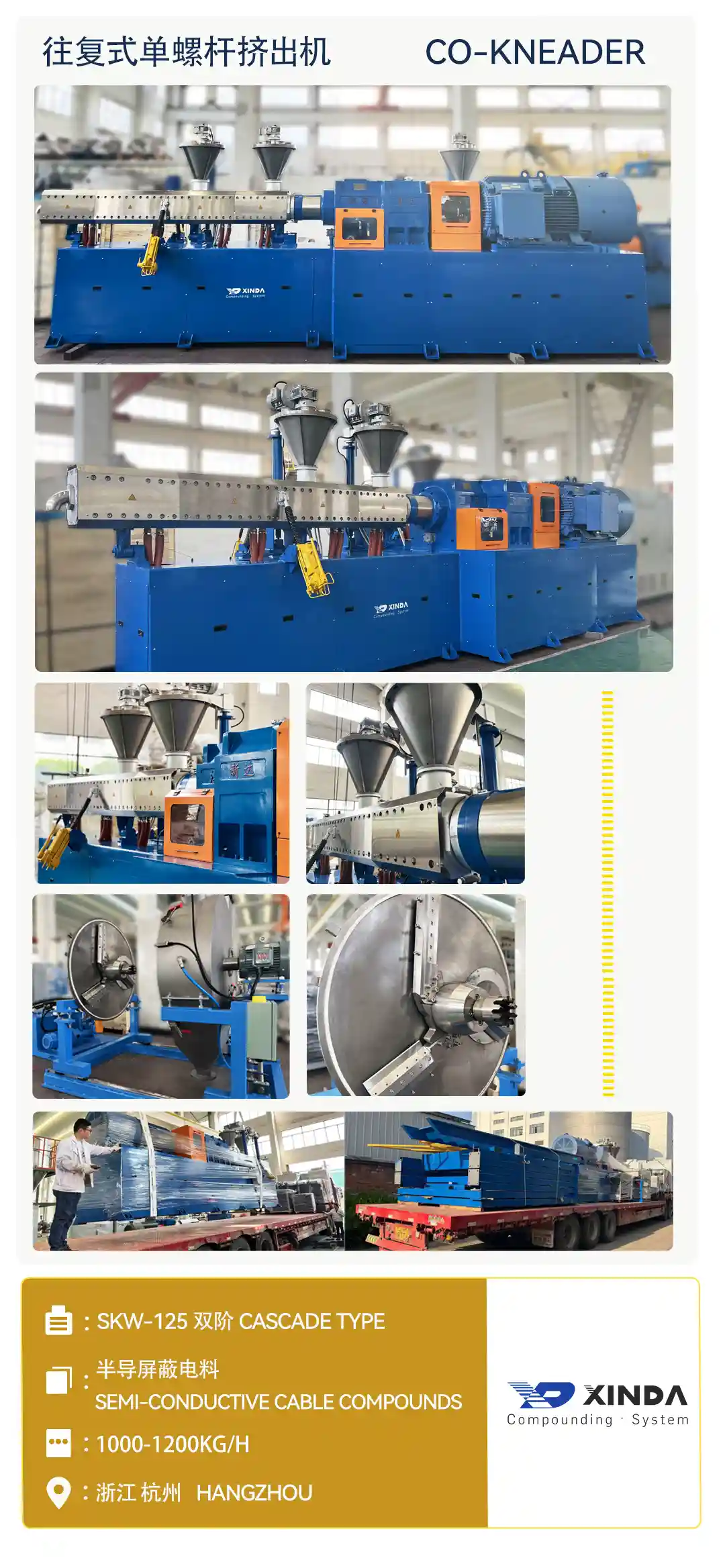
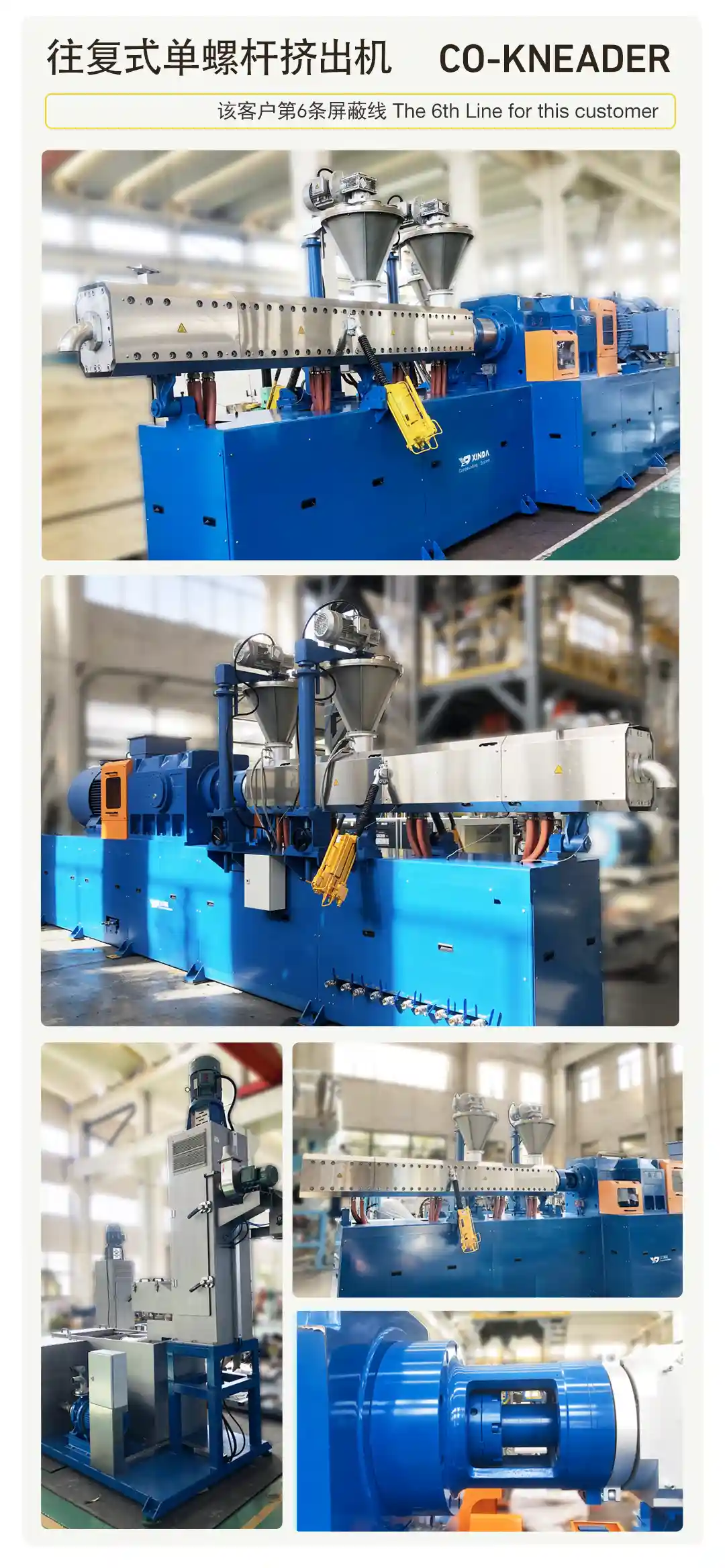
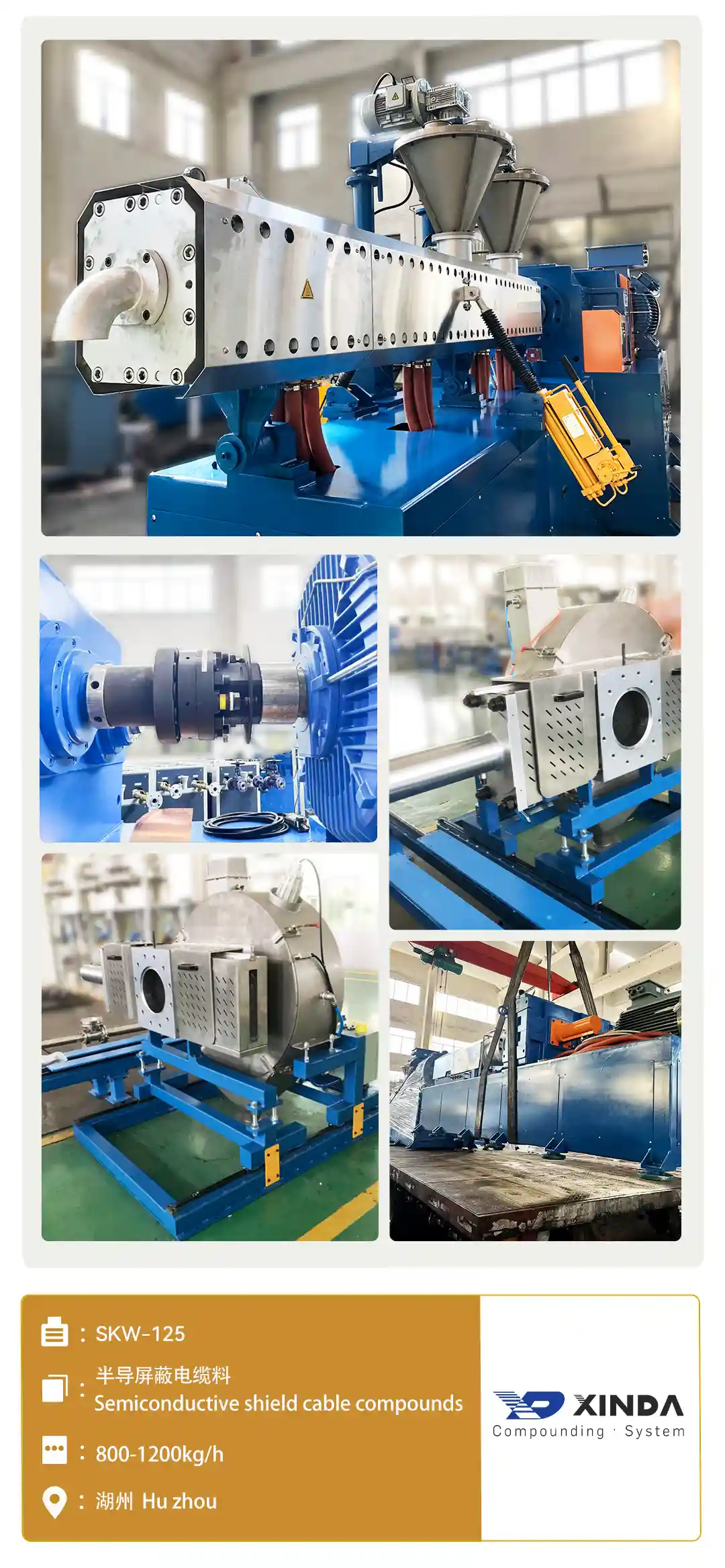
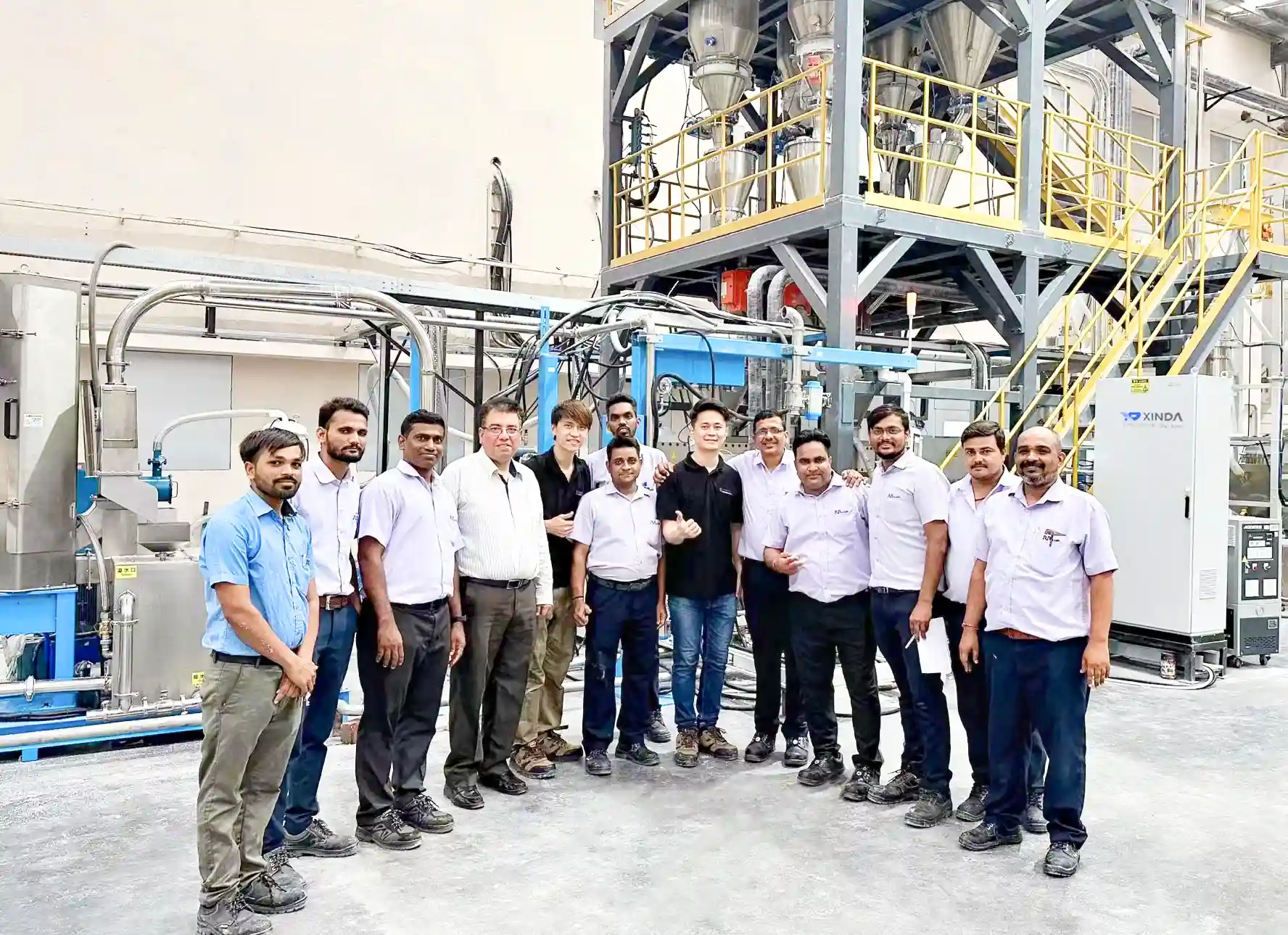