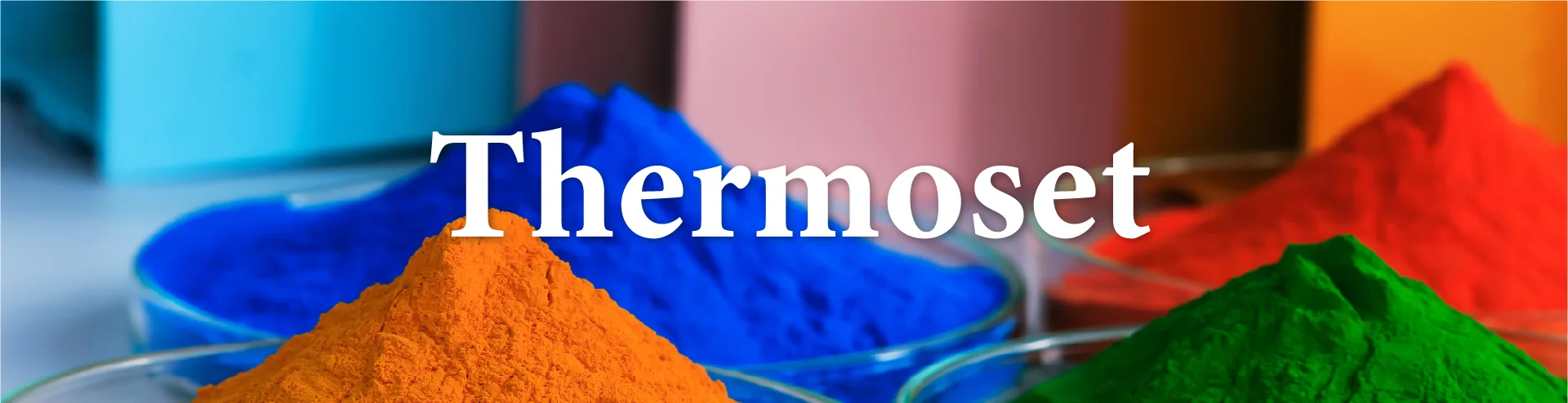
Compounding technology for Thermosets
Compounding technology for thermoset extrusion involves the process of combining various additives and reinforcing agents with thermosetting resins to enhance their properties and make them suitable for specific applications. Thermosetting resins are a class of polymers that, once cured, cannot be melted or re-molded, making them ideal for high-performance applications where heat resistance and dimensional stability are critical.
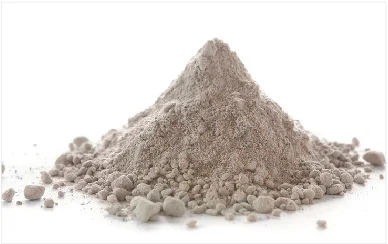
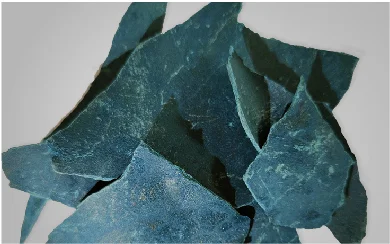
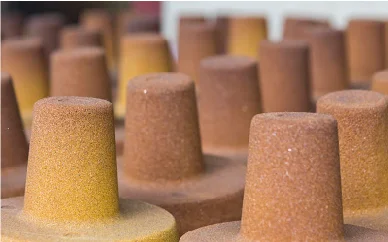
The compounding process for thermoset extrusion typically involves several steps, including:
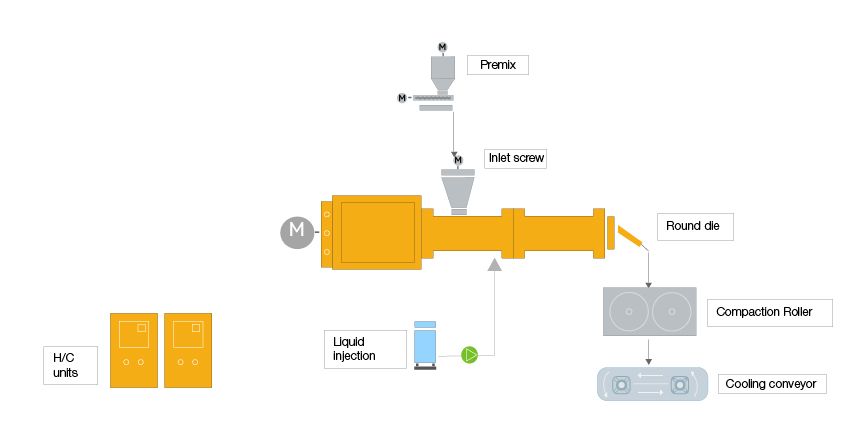
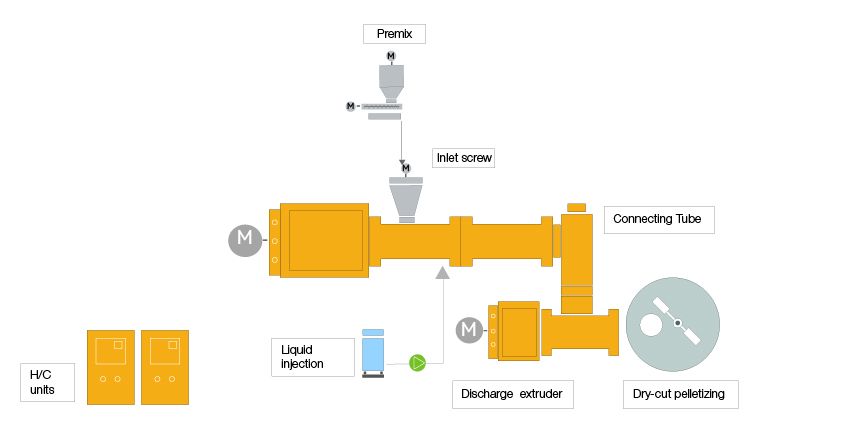
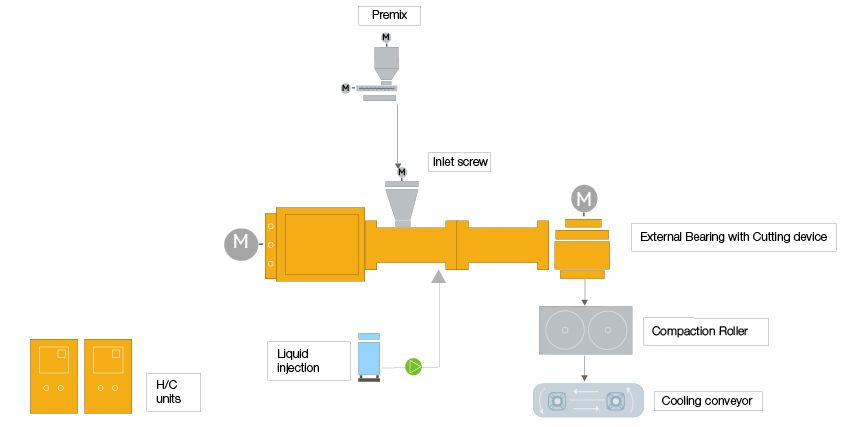
Resin selection:
The choice of resin depends on the desired properties of the final product. Common thermosetting resins include epoxy, phenolic, and melamine.
Additive selection:
Additives such as curing agents, catalysts, and flame retardants are selected based on the resin system and the application requirements.
Mixing:
The resin and additives are mixed using specialized equipment such as a Banbury mixer, sigma mixer, or kneader. The mixing process must be carefully controlled to ensure the uniform dispersion of additives and the proper curing of the resin.
Degassing:
The compounded material is degassed to remove any air pockets that may have formed during mixing. This step is critical for ensuring the quality and consistency of the final product.
Extrusion:
The degassed compound is extruded into a continuous shape such as a sheet, rod, or tube, or molded into a specific shape using injection molding or compression molding.
>>
The compounding technology for thermosets allows for the production of materials with superior mechanical, electrical, and thermal properties, making them suitable for a wide range of applications in industries such as aerospace, automotive, electronics, and construction.
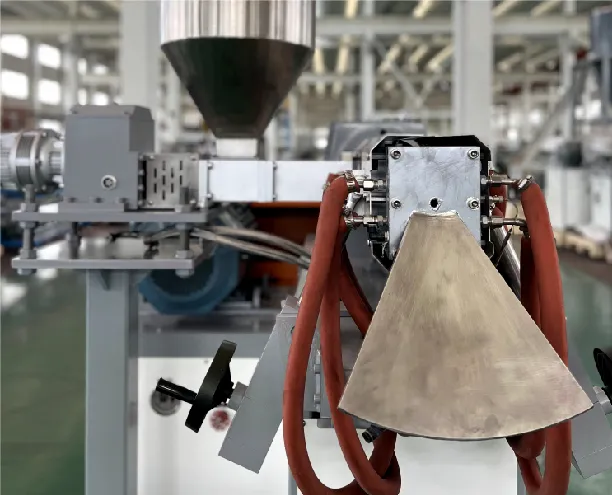
Xinda Co Kneader
thermoset compounding systems offer several specific benefits
> Efficient mixing:
The co-kneader design provides high shear mixing, ensuring efficient dispersion of additives and reinforcing agents throughout the thermoset resin.
> Consistent quality:
The efficient mixing and precise temperature control of XINDA Co-kneader systems ensure consistent quality and uniformity of the compounded material.
> Precise temperature control:
XINDA Co-kneader systems feature advanced temperature control systems that allow for precise temperature control during the compounding process. This is critical for ensuring the proper curing of the thermoset resin.
> Reduced energy consumption:
XINDA Co-kneader systems are designed to operate at high efficiency, reducing energy consumption and operating costs.
> Flexible processing:
XINDA Co-kneader systems are capable of processing a wide range of thermosetting resins, including epoxy, phenolic, and melamine. They can also process various additives and reinforcing agents, making them highly versatile.
> Reduced waste:
The efficient mixing process of XINDA Co-kneader systems results in less waste and scrap material, reducing production costs.
> High throughput:
The co-kneader design enables high-volume production, making XINDA Co-kneader systems ideal for large-scale thermoset compounding applications.
> Improved product properties:
XINDA Co-kneader systems can incorporate additives and reinforcing agents into thermoset resins, improving the mechanical, thermal, and electrical properties of the final product.
> Overall:
XINDA Co-kneader thermoset compounding systems offer a highly efficient and flexible solution for producing high-quality thermoset compounds with enhanced properties.
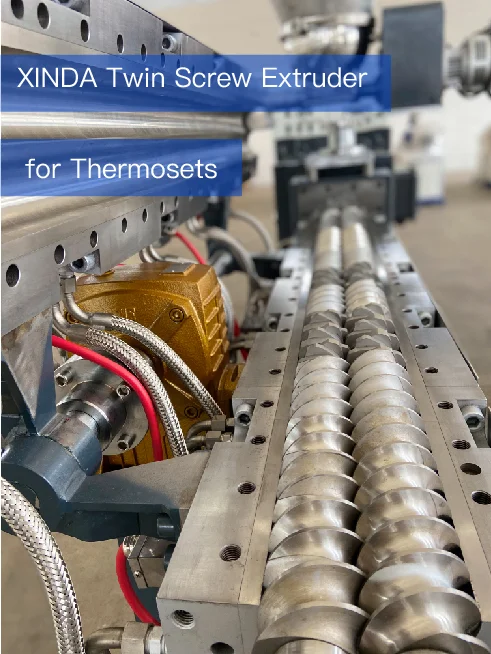
Why Xinda’s Twin Screw Extruder different?
> Clamshell Barrel:
Clamshell Barrel: The barrel can be quickly opened for cleaning and maintenance. According to material variety and different technological requirements,it can be flexible combined into an ideal structure to improve the overall utilization rate of the equipment.