Application: Final batch Rubber (for rubber seals), one of the largest pipe seal manufacturers in Europe
Nation: Germany
Equipment: XINDA machine: 3-flight Co-kneader SJW-200

1. In 2011, the customer discussed the new production process of their products with XINDA, and both parties determine to cooperate in R & D. During this period, they adjusted the production process in Xinda laboratory for many times and took it back to Germany for repeated tests. The final product quality exceeded the original.
2.In 2012, the customer purchased xinda co-kneader SJW-200 to produce final batch rubber for rubber seal products, changing the processing technology of traditional banbury kneaders and milling rollers, which greatly improved the stability of product performance. At the same time, high degree of automation of Co-kneader improved the workshop production environment. The capacity per unit compounding line can reach 10,000 tons/year.
Customer’s Feedback and Review
1. Low shear and high dispersion is the unique characteristic of Co-kneader. Raw materials, like rubber particles, carbon black, white oil, rubber accelerant and curing agent and so on, enter in turn on the reciprocating machine in sections, with accurate material temperature control, sufficient dispersion and mixing, excellent product performance and good product homogeneity and stability.
2. Degree of automation of Co-kneader in production is extremely high. Raw materials can be divided into groups and metered into sections through gravimetric feeding system. The rubber particles, carbon black, white oil, and vulcanizing agent are fed in a closed manner. So the workshop production environment is quite clean.
3.Three-flight Co-kneader SJW-200 has high production capacity and low energy consumption. Compared with the traditional internal refining plus open refining production equipment, the energy consumption per ton is reduced by 20% – 30%.
4. The upper-stage reciprocating machine adopts a clamshell barrel design, while screw of the second-stage pelletizing extruder can be separated by pulling back. Therefore, when formulas change or the machine needs maintenance, it can be quickly opened and cleaned, which shortens the time of conversion and maintenance.
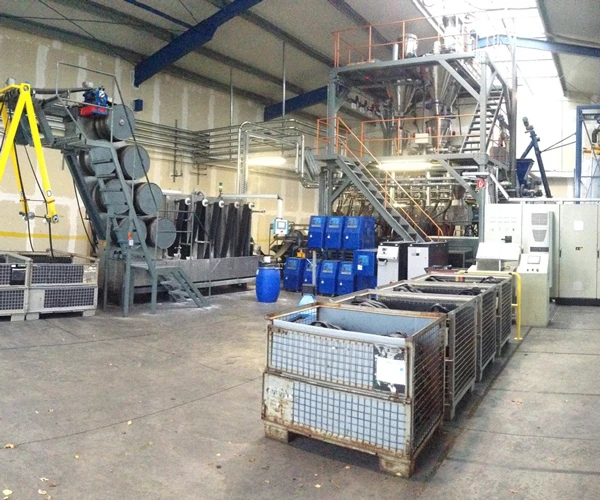
