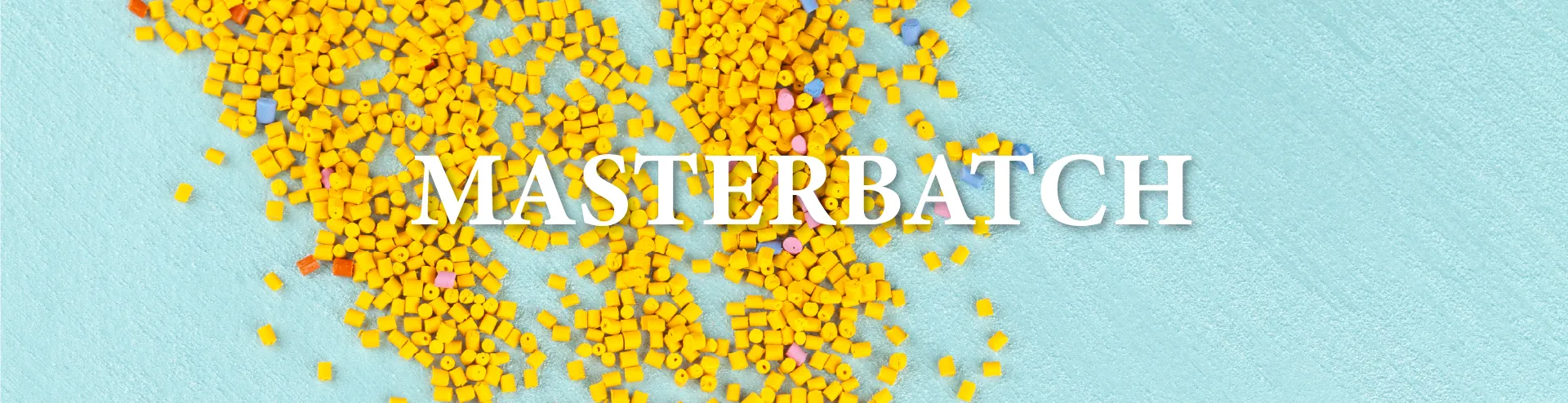
Compounding Systems for Masterbatch
Masterbatch compounding is the process of combining various raw materials, such as pigments, additives, and resins, to create a concentrated mixture that can be used as a coloring or functional additive in various polymer applications. The process of creating masterbatch compounds involves several steps that are aimed at achieving a uniform distribution of the individual components within the final product.
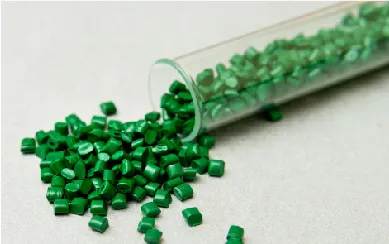
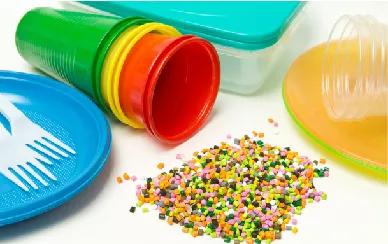
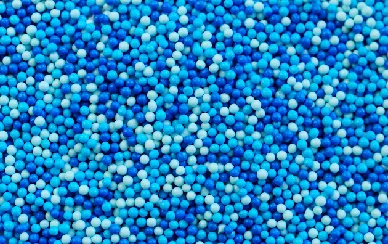
Here is a detailed description of the compounding system for masterbatch:
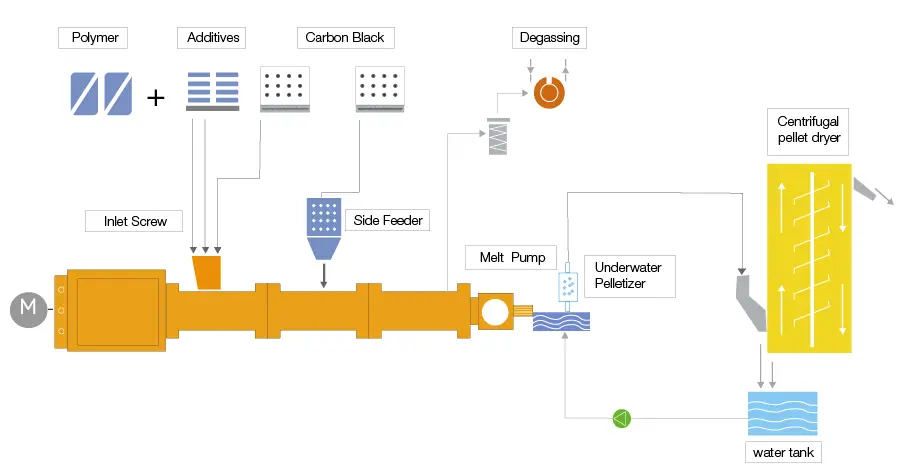
Raw Material Handling:
The first step in the masterbatch compounding process is to handle the raw materials that will be used to make the compound. These materials are typically in the form of pellets, powder, or liquids and are stored in silos or containers until needed. The raw materials are weighed and blended according to the desired formula.
Mixing:
The next step is to mix the raw materials together. This is typically done in a high-intensity mixer, which ensures that the materials are thoroughly blended and any additives are well-dispersed. The mixing time and speed depend on the type of mixer and the specific requirements of the masterbatch formulation.
Extrusion:
After mixing, the compound is fed into an extruder, which melts and homogenizes the mixture. The extruder has a screw that rotates and pushes the molten compound through a die, which shapes the compound into the desired form, such as pellets or strands.
Cooling and Cutting:
Once the compound is extruded, it is cooled and solidified using air or water. The solidified compound is then cut into the desired length, typically in the form of pellets.
Quality Control:
The final step in the compounding process is quality control. The pellets are checked for color, consistency, and other properties, such as melt flow and particle size distribution. The masterbatch must meet the required specifications before it can be packaged and shipped to the customer.
Overall:
The compounding system for masterbatch involves precise handling of raw materials, thorough mixing, extrusion, cooling, and quality control to ensure a high-quality product. The process is highly automated and requires skilled technicians to ensure consistency and accuracy.
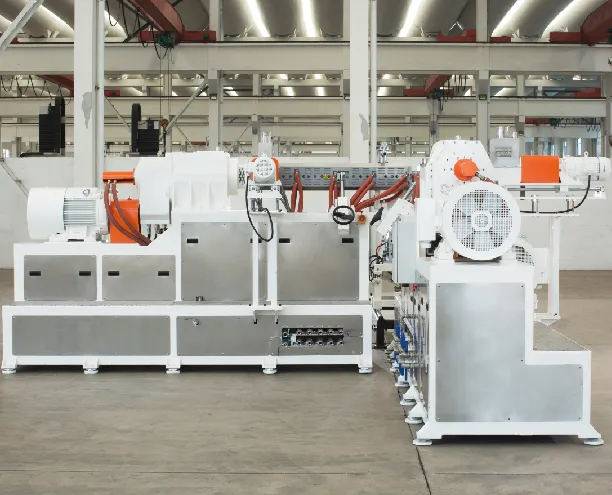
Xinda Co Kneader
Masterbatch compounding system
offer several specific benefits
> Efficient mixing:
Co-kneader technology uses a unique design that enables high shear mixing and efficient dispersion of materials, resulting in a homogeneous and consistent product.
> Reduced waste:
The efficient mixing process of co-kneader systems results in less waste and scrap material, reducing production costs.
> High throughput:
These machines can handle large volumes of materials, enabling the production of high-quality masterbatch in large quantities.
> Improved product properties:
Co-kneader systems can incorporate additives and fillers into the masterbatch, improving the mechanical, thermal, and processing properties of the final plastic product.
> Consistent quality:
The co-kneader design ensures that the mixing process is consistent and repeatable, resulting in a uniform product.
> Process control:
Co-kneader systems offer precise control over the mixing process, allowing for adjustments to be made in real-time to achieve the desired product properties.
> Flexibility:
These systems can process a wide range of materials, including thermoplastics, elastomers, and rubber compounds.
> Energy efficiency:
Co-kneader systems are designed to operate at high efficiency, minimizing energy consumption and reducing operating costs.
> Split barrel:
The barrel can be quickly opened for cleaning and maintenance. According to material variety and different technological requirements,it can be flexible combined into an ideal structure to improve the overall utilization rate of the equipment.Especially for color master batch industry.
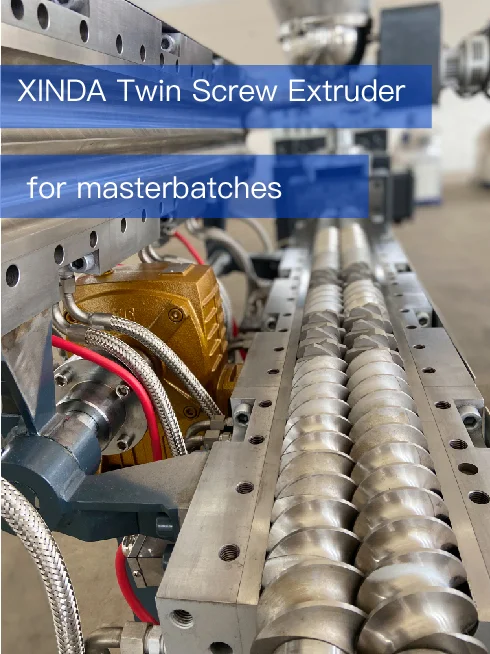
> Clamshell Barrel:
The barrel can be quickly opened for cleaning and maintenance. According to material variety and different technological requirements,it can be flexible combined into an ideal structure to improve the overall utilization rate of the equipment.Especially for color masterbatch industry.