
Introduction to Pharmaceutical Blending
The pharmaceutical industry has learned processing technology from plastic blending to form a unique pharmaceutical blending method. In turn, we learned a lot about the twin-screw extrusion process from the pharmaceutical process. For example:
I.
Pharmaceutical TSE pays more attention to regulations and guidance documents, especially the dynamic pharmaceutical manufacturing practice (cGMP) used in pharmaceutical operations, which can make manufacturing more stable, reproducible, and more efficient. In today’s pursuit of intelligent manufacturing, these normative measures are very meaningful, because standardized operations are the basis and premise of intelligence.
II.
The preference for certain types of TSE, such as the preference for counter-rotating intermeshing twin-screw extruders, is an interesting phenomenon that deserves analysis.
The emphasis on some plastic TSE technologies, such as the re-examination of the starvation feeding function, we may be able to learn on PP devolatilization and odor reduction. The experience of avoiding excessive shearing of feeding materials at the back end of the processing area is inspiring for light-diffusing plastics.
Twin-Screw Extrusion Process in Pharmaceuticals
Twin-screw extrusion process has been the standard process for plastics compounding for decades, but it has only been accepted by the pharmaceutical industry in recent years. Here’s what plastic compounders can learn from our little brother, the drug maker, to help us make better, more consistent products.
Leading development activity in the late 1980s and 1990s resulted in several commercial drug delivery components that rely on TSEs. Driven by the FDA’s Process Analytical Technology activities, twin-screw extruders have since become accepted by most world-class pharmaceutical companies.
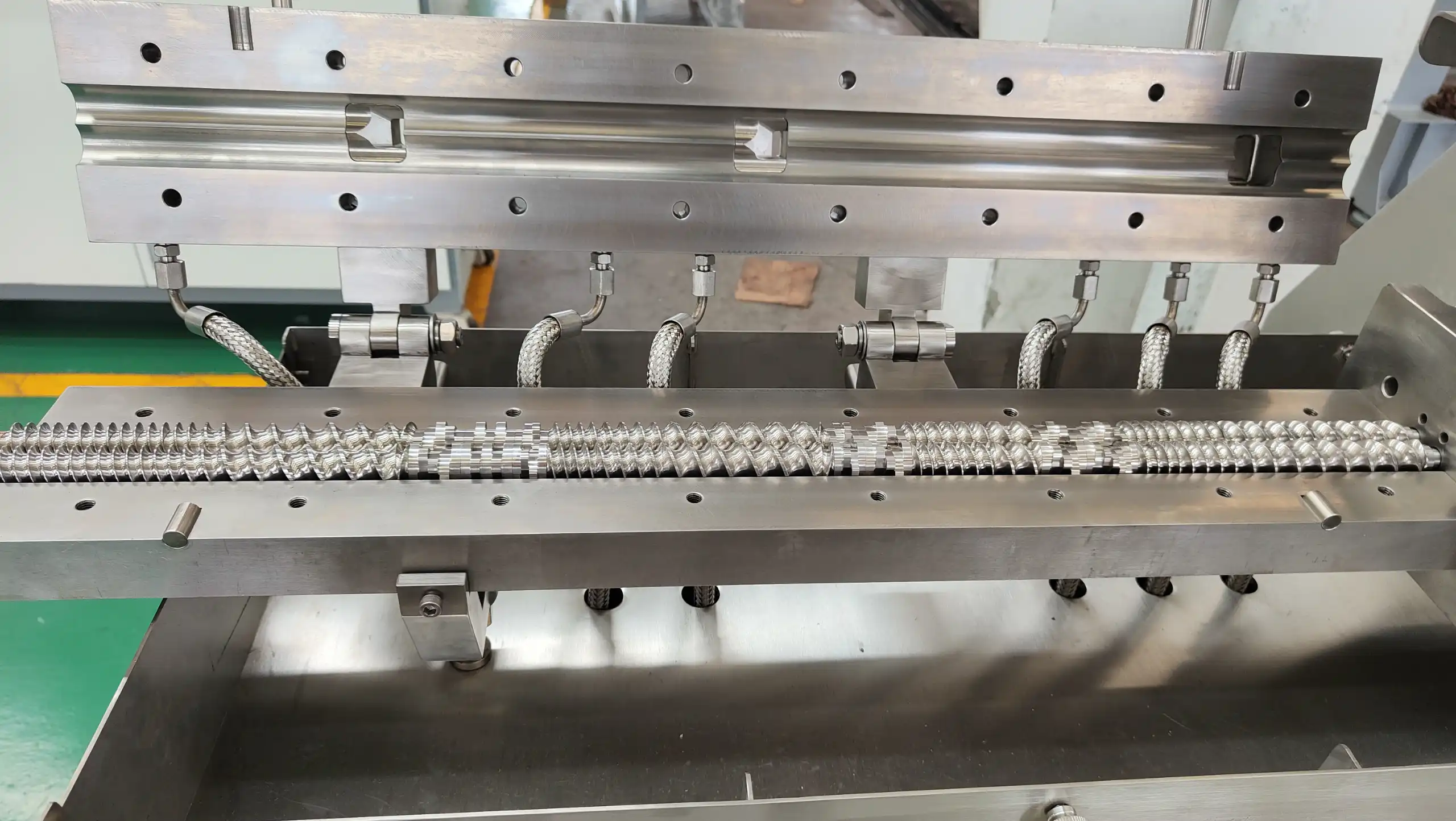
In history, most drug delivery formulations have been manufactured through compounding processes. The FDA’s 2004 PAT activity provides drug manufacturers with a framework to guide drug development, manufacturing, and quality assurance through online monitoring. In short, PAT activities strongly encourage that new agents should be developed and manufactured through continuous processing with on-line monitoring of key parameters. This file could simply have been written by an extruder supplier.
Fundamentals of Twin-Screw Extrusion Process
Twin-screw extrusion process material in a channel that is connected adjacently by the screw and the barrel wall, so it is called a small-batch continuous mixer. The motor inputs energy into the process, and the mixing is carried out by rotating the screw. Process control parameters include screw speed (rpm), feed rate, temperature along the barrel to the die, and exhaust vacuum. Typical parameters that are monitored for in-line quality measurement include melt pressure, melt temperature, motor current, and in-line IR sensors. Programmable logic controllers (PLCs) and touchscreen human-machine interfaces (HMIs) are now commonplace equipment compared to the older isolated controls and instrument readouts.
Advanced TSE Design and Configuration
The basic design of a TSE for plastics or pharmaceuticals is the same. The mixing principle and unit operation segmentation are essentially the same. TSE processing technologies proven in industrial processing facilities can often be quickly implemented in pharmaceutical processes—TSE processing is a definite given.
TSE utilizes segmented threads assembled on high torque screw shafts. The barrel is also modular and integrated with internal bores for barrel cooling. The segmented screw and barrel, combined with the controlled pumping and self-cleaning characteristics of the co-rotating screws, allow the screw/barrel geometry to be matched to the processing task. The counter-rotating intermeshing twin-screw pattern is also used for processing PVC, masterbatches and pharmaceutical compounding applications.

Efficient Mixing and Volatile Removal
Compared with large-volume reciprocating mixers, TSE’s inherent high-intensity mixing and short-time mass exchange characteristics between the screws are conducive to efficient mixing operations. Trapped air, moisture, and volatiles are removed by vacuum exhaust during the extrusion process. The relatively short residence time (1 second to 2 minutes) in the TSE is advantageous for many heat and shear-sensitive materials because the TSE can be designed to limit its exposure to high temperatures to only a few seconds.
TSE uses starvation feeding. The production rate is determined by the feeder. The feeder meters pellets, liquids, powders, and fibers to the processing section. TSE screw speed does not depend on feed rate. This allows for optimal blending efficiency. Some APIs, like pigments, need dispersive mixing in TSE. Others benefit from distributive mixing. A shear-sensitive API or pigment can be metered at the back end of the processing section. This avoids high shear strength under melt conditions.
As a key process parameter to be monitored (depending on whether it is a plastic blend, masterbatch, or formulation) specific energy (SE) is defined as the energy input to the unit mass of material being processed. If there is a sudden change of SE, it means, equipment, process conditions, or raw materials have changed, and the end product may become different.
KW(real-time)= KW (motor power) X % torque X RPM(rinning) /maximum
RPM X 0.97 (gearbox efficiency)
SE=KW (real-time) / (kg/hr)
Unit:
SE is marked as KW per kg/hr
KW=kilowatt (motor power in KW=HPX0.746)
%Torque = percentage of maximum allowable torque usage
RPM=screw rotation speed/minute
Downstream System and Applications
The downstream system of pharmaceutical equipment is also similar to plastics. Strand and die face pellets are used for water-soluble pharmaceutical products. In addition to water, the particles are also annealed on the conveyor belt, or transported and cooled in air to facilitate granulation. Smaller particles can be used for direct microencapsulation filling, while larger particles are generally ground and compressed into tablets. Laminated systems are used for subcutaneous and insoluble film applications. Tubing systems produce antimicrobial structures, while coextruded rods are integrated into contraceptive devices (e.g. vaginal rings). Such applications are infinite.
Compliance with cGMP and FDA Part 11
TSEs in a cGMP environment comply with FDA Part 11 of Title 21 of the CFR on Electronic Records and Electronic Signatures. Part 11 sets standards for honest and reliable electronic records. It requires drug manufacturers to implement controls, audits, and system verification of electronic data processing software and systems. Parameters must be verified and periodically calibrated, which is a good practice for extrusion installations.
Protocols and Device Validation
Protocols must limit access to the system to authorized individuals and implement operational and equipment verification. Strict adherence to methods for copying and retaining records is part of the guidelines.
Device validation documentation in a pharmaceutical-grade environment is more elaborate than in typical plastic devices. Pharmaceutical-grade installations take months to complete, requiring detailed documentation packages (FAT), installation qualification (IQ), and operational qualification (OQ).
Cleaning Guidelines and Benefits to Plastics Industry
cGMP guidelines for cleaning pharmaceutical-grade TSE systems specify equipment must be cleaned at appropriate intervals according to documented procedures. After cleaning, equipment is protected from contamination and checked for cleanliness before use. Records and logs of all clean-ups and inspections must be kept, and the time between processing and clean-out recorded.
A similar protocol would benefit plastics processing operations. Pharmaceutical TSE manufacturing units require more controlled and documented approaches than standard plastics industry activities. While not all FDA guidelines can apply to plastic blends, auditing pharmaceutical manufacturing practices selectively may be useful. This helps create more stable and repeatable products.”
Content source: PTonline, Xintec Translation
Disclaimer: (Part of) the data, charts, or other content in this article comes from the Internet or other publicly published materials, and is for readers’ reference, communication, and learning only, and does not involve any commercial behavior or purpose. The copyright belongs to the original author and original source. If the copyright owner believes that this article is suspected of infringement or other problems, please contact us and deal with it in time.