Twin screw extruders are commonly used in plastic production processing. In actual production processes, they leverage their inherent performance advantages to enhance the utilization of material resources and reduce material residue within the extruder. As the scale of production processing continues to expand, the modified plastic production processing industry is demanding higher-level performance from twin screw extruders.
Improvements in the cooling box and side feeding device of the twin screw extruder can effectively enhance its production efficiency.
extruder is accomplished by adjusting the frequency of the main motor. Supported by support rods, the distance between plastic products and the contact box is reduced, preventing adhesion occurrences and effectively meeting practical production needs. This realizes the goal of enhancing the quality of plastic product production, ensuring product production diversification, and broadening the application scope and domain of twin screw extruders.
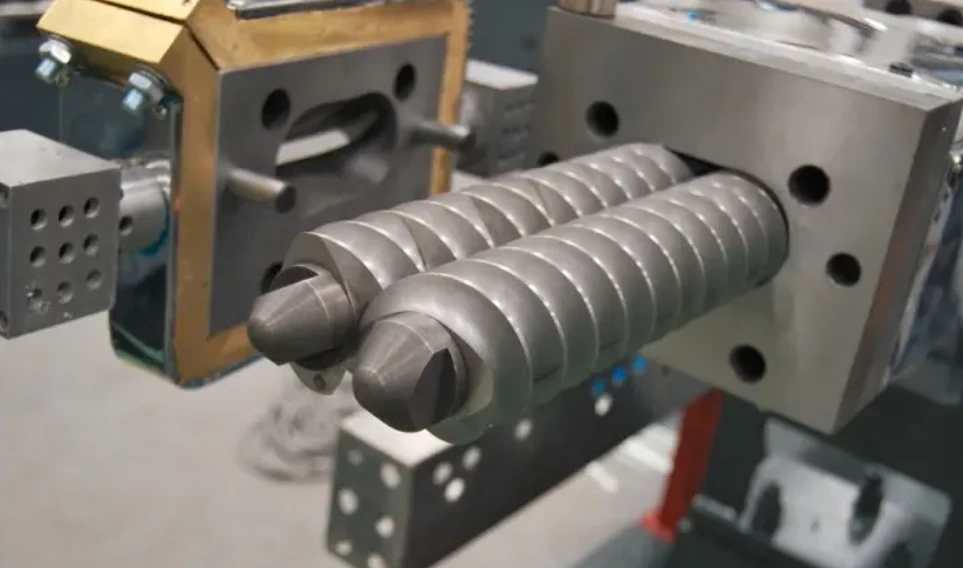
① Reduction of Air Entrapment during Filling
The addition of exhaust ports upstream of the side feeding port facilitates the replacement of the original screws with lead screws. The side feeding hopper is divided into two parts: the front part for exhaust and the rear part for feeding.
The addition of exhaust ports upstream of the side feeding port facilitates the replacement of the original screws with lead screws. The side feeding hopper is divided into two parts: the front part for exhaust and the rear part for feeding.
② Preservation of Free Space at One Side of the Feeding Port
Increasing free space at one side of the feeding port meets actual filling volume requirements. Based on this, large lead screw components are designed on the existing screw foundation. Asymmetric screw elements are placed upstream of the combined screw side feeding port. A reverse conveying element is incorporated on one side of the screw side feeding port, while a reverse grooving element is designed on the other side. During material transport, when the material reaches the
asymmetric element in a molten state, significant distribution changes occur under the action of the asymmetric element. One side of the feeding port undergoes reverse conveying while the other side simultaneously undergoes reverse conveying. In the process of material reverse conveying, one side of the feeding port forms a cavity under the action of the reverse conveying element, significantly increasing the filling volume of the side feeding device.
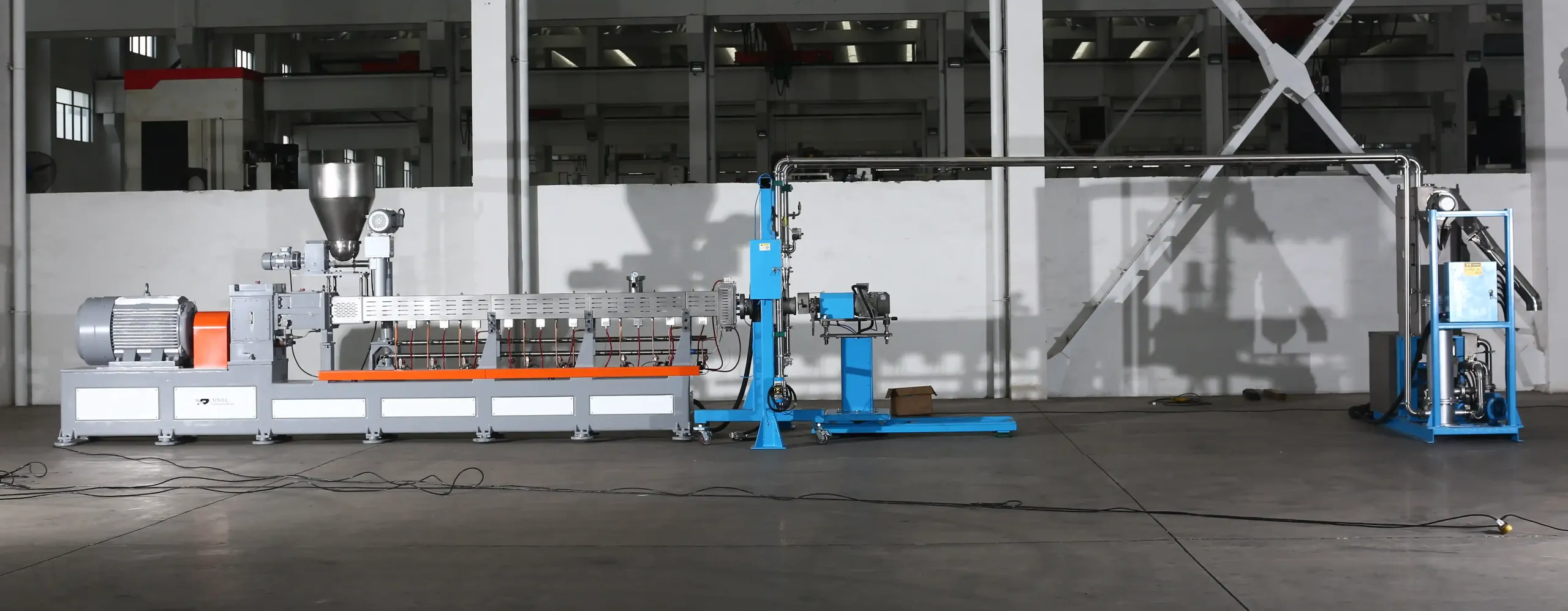
③ Dual Feeding System
Transforming the original single feeding mode into a dual feeding port simultaneous feeding mode forms a “Dual Feeding System.” During the actual transformation process, it was discovered that the pads under the feeding system shifted under vibration. In the secondary transformation,
fixed supports were added, effectively solving the vibration displacement issue, optimizing the filling process and links, and achieving high-quality production and processing of products with the main material mixed, extruded, and sheared at a certain temperature.
Disclaimer: This article’s data, charts, and content are sourced from the Internet or publicly published materials. They are for reference, communication, and learning only, with no commercial intent. Copyright belongs to the original authors and sources. If any copyright owner believes this article infringes on their rights, don’t hesitate to get in touch with us for a timely resolution.