Liu Boyuan
China Plastics Association Modified Materials Committee
Beijing 230022
Kong Xiangming
Jiangyin Xinda Plastic Machinery Co., Ltd
214407
Liu Yingjun
China Plastics Association Modified Materials Committee
Beijing 10037
Keywords:
reciprocating single screw compounding extruder structure application
Abstract:
China’s first SJW-70 reciprocating single screw compounding extruder was successfully developed in 2000. This technology is internationally advanced and fills a domestic gap. The advent of this machine not only ended my country’s long-term dependence on imported Buss Kneader compounding extruders, but also brought my country’s plastic machinery processing level close to the world’s advanced level.
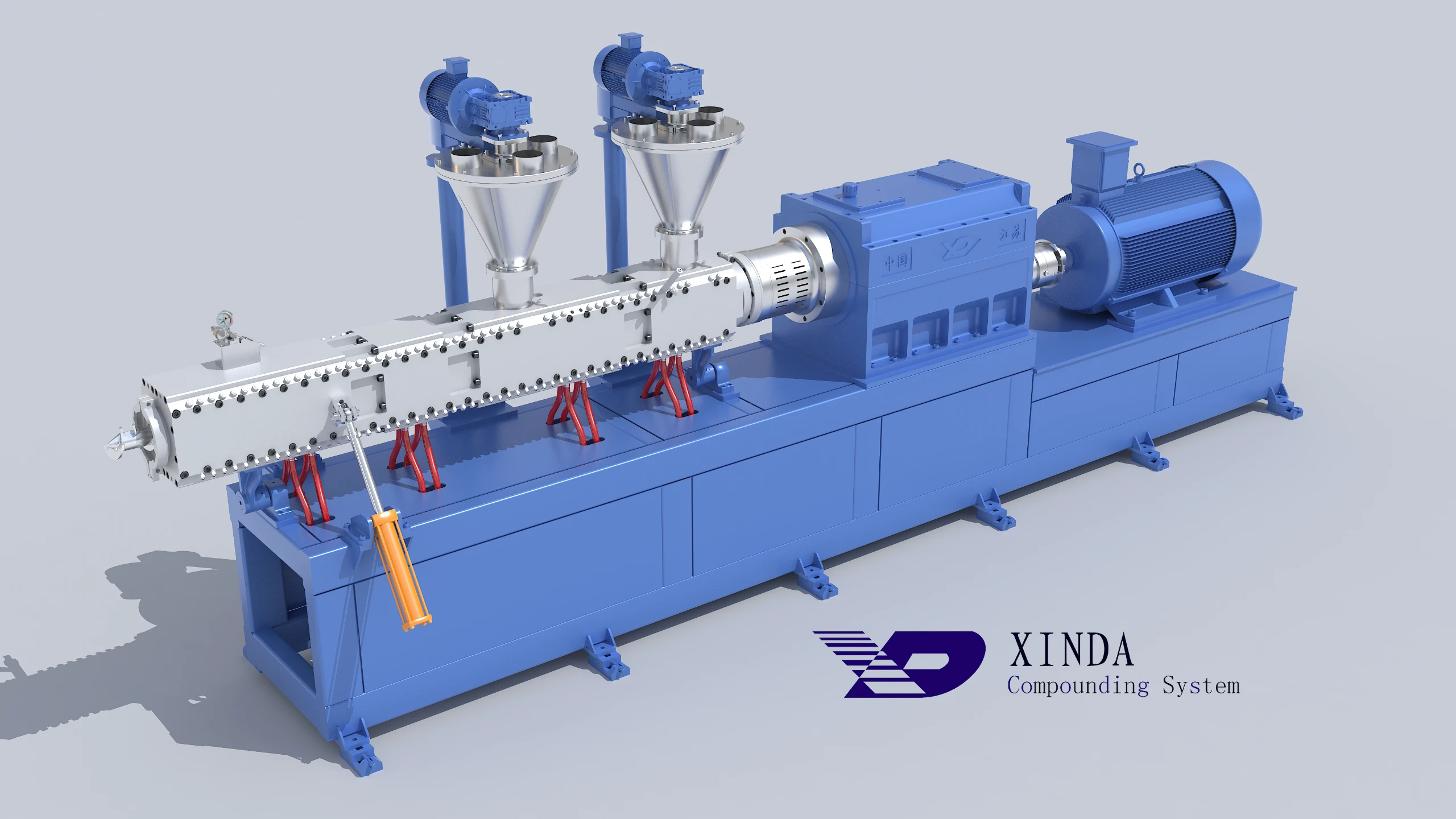
1. Overview
Jiangsu Xinda Tech Limited has successfully developed China’s first SJW-70 reciprocating single screw compounding extruder. It has been put into the company’s production of black or colored masterbatches for polyester and polyolefin fibers. It also has been running continuously for more than ten months, and the machine is running stably. The various masterbatches produced are evenly dispersed in the matrix resin, especially the black masterbatch with a carbon black concentration of 30%, which is evenly dispersed in the black chemical fiber.
The structural features of the machine are: the threads on the screw are not continuous, and the threads are interrupted three times per turn. The barrel is split and can be opened for rapid cleaning of materials; three rows of kneading pins are installed on the inner surface of the barrel according to a certain pattern, which can be adjusted and replaced; the pins with holes can be equipped with sensors. The screw elements are mounted on the screw shaft in the form of the segmented type according to different uses, and the barrel can be heated or cooled, etc.
The working principle of this machine is: the screw rotates continuously and also makes an axial reciprocating motion according to a certain rule, to diversify the movement of materials between the screw and the barrel. The fixed pin on the barrel is like a second screw, which has the functions of cleaning the screw ribs, conveying and distributing materials, and dispersing and mixing. The material mixing can occur in the axial direction, which is different from single-screw or twin-screw extruders. The mixing, kneading, and self-cleaning effects of this machine are good.
The main parameters of this machine are screw diameter: 70mm; screw length diameter ratio (L/D): 20:1; screw speed 40~350 rpm; main motor power: 75KW; production capacity can reach 100~350kg/h depending on the material.
In the past, no company in our country could manufacture Buss Kneader-type mixing extruders. Now Jiangyin Xinda Polyester Plastic Co., Ltd. has successfully trial-produced this type of mixing machine, and it was approved by experts from the State Light Industry Bureau and Jiangsu Provincial Science and Technology Commission on July 10, 2000. The machine was exhibited during the 14th International Plastics and Rubber Industry Exhibition (Shanghai, July 4-8, 2000), attracting thousands of visitors.
2. Structure
The structure of the SJW-70 reciprocating single screw compounding extruder is very different from that of an ordinary twin-screw extruder (as shown in Figure 1). The threads on the screw are not continuous. The threads are interrupted three times for each turn of the screw
The barrel is split and can be opened quickly to clean the material. Its inner surface is equipped with three rows of kneading teeth in a certain pattern. These teeth can be adjusted and replaced. Some teeth are hollow to install sensors. The screw is composed of different components and is mounted on the mandrel in the form of segmented type. The barrel has a liner, and both are heated or cooled with liquid media.
Figure 1: Comparison between ordinary single screw and reciprocating single screw
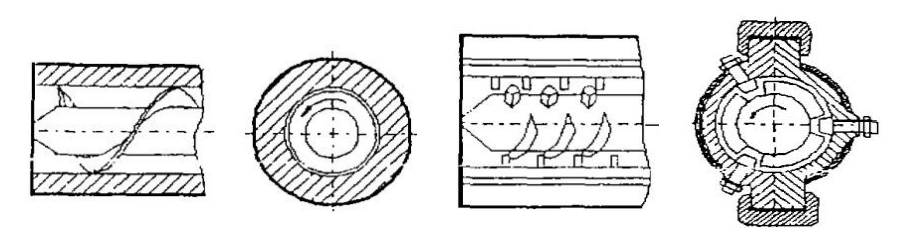
(a) Ordinary single screw
(b) Reciprocating single screw
3. Working Principle
The main difference between the SJW reciprocating compounding extruder and conventional twin-screw and single-screw extruders is that the screw rotates continuously and also performs axial reciprocating motion according to a certain rule.
This greatly complicates the movement of the material in the screw and barrel. In addition to the normal flow of the material in the wedge-shaped area, a small part of the material flows back to form a drag flow. As shown in Figure 2 below.
Figure 2: Material flow in the wedge zone
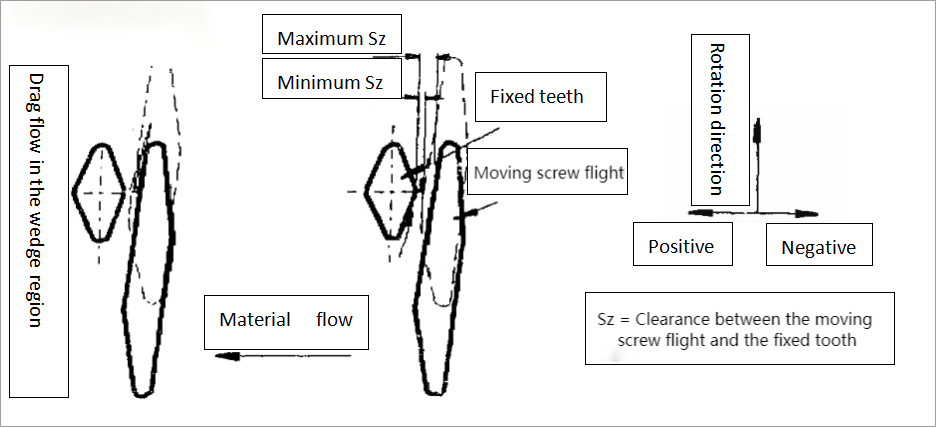
The fixed teeth on the cylinder act as a second screw, which has a great effect, cleaning the screw fins, conveying the material, and distributing and mixing the material. It is different from conventional screw extruders in that the mixing action occurs in the axial direction rather than in the radial direction.
4. Extrusion process
The complexity of the structural movement of the reciprocating extruder makes the extrusion process in it different from that of the conventional screw extruder.
Material conveying: After the material is added to the screw, the rotation and reciprocation of the screw compacts the material. The screw is discontinuous, and the air entrained in the material returns to the feed port for discharge. The waste gas in the melt is discharged from the exhaust hole.
Melt conveying: The material in the barrel begins to melt. Due to the reciprocating and rotating movement of the screw, the melting process will not form a solid bed, a molten pool or a ring like in a conventional extruder, and the melting that drags the melt away will occur. The teeth on the barrel pass through the discontinuous threads on the screw, and the melted material leaves the inner surface of the barrel and is pulled into the unmelted material. At the same time, the unmelted material is brought to the inner surface of the barrel. In this way, the melted and unmelted materials are mixed, the wetted surface is increased, and the total heat transfer area is increased.
5. Distributive mixing and dispersed mixing of materials by reciprocating single screw extruder
In conventional screw extruders, materials rarely re-orient, so the distribution and mixing are not good. The reciprocating single-screw extruder changes the thin layer shearing law of conventional extruders. The barrel is equipped with teeth, which can continuously cut and produce new material surfaces so that the materials can be oriented, cut, folded, re-oriented, etc., and obtain a good mixing effect. The shearing process of one screw rotation is shown in Figure 3 below.
Figure 3: The meshing process of the screw and the teeth after one rotation
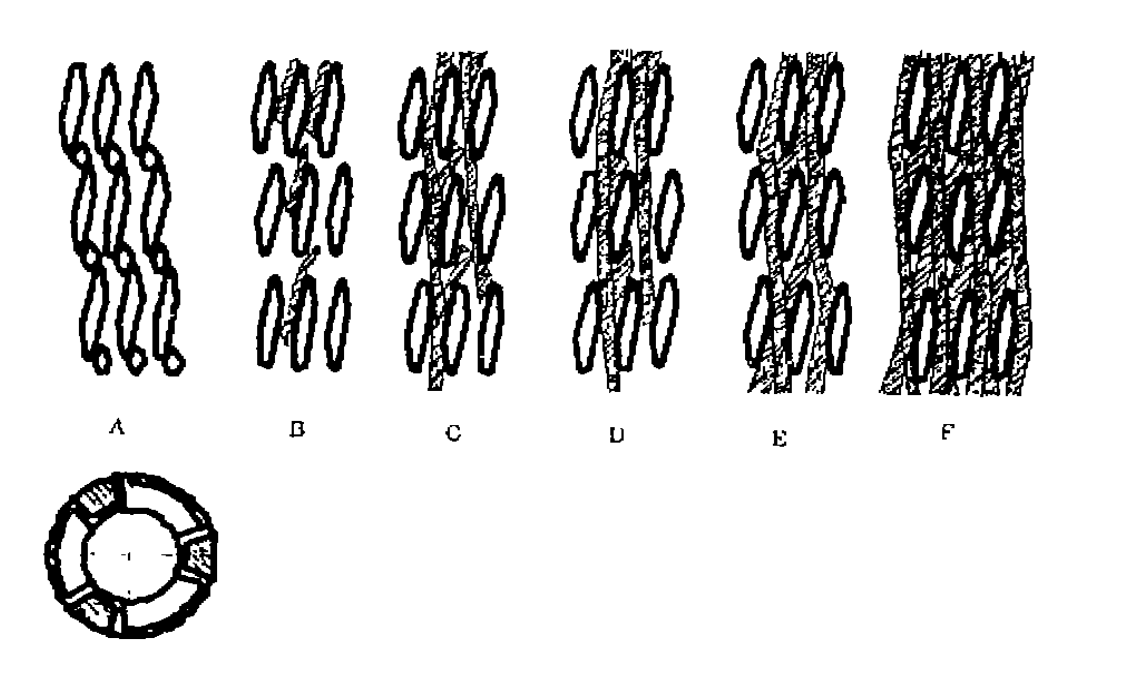
The dispersion mixing of reciprocating single screw extruders is also different from that of conventional extruders. The mixing action of the conventional extruder occurs radially, while the mixing of the reciprocating single screw extruder is realized in the axial direction, between the moving screw thread and the fixed teeth, which can make all the materials in the screw groove receive uniform shear stress. As shown in Figures 4 and 5 below.
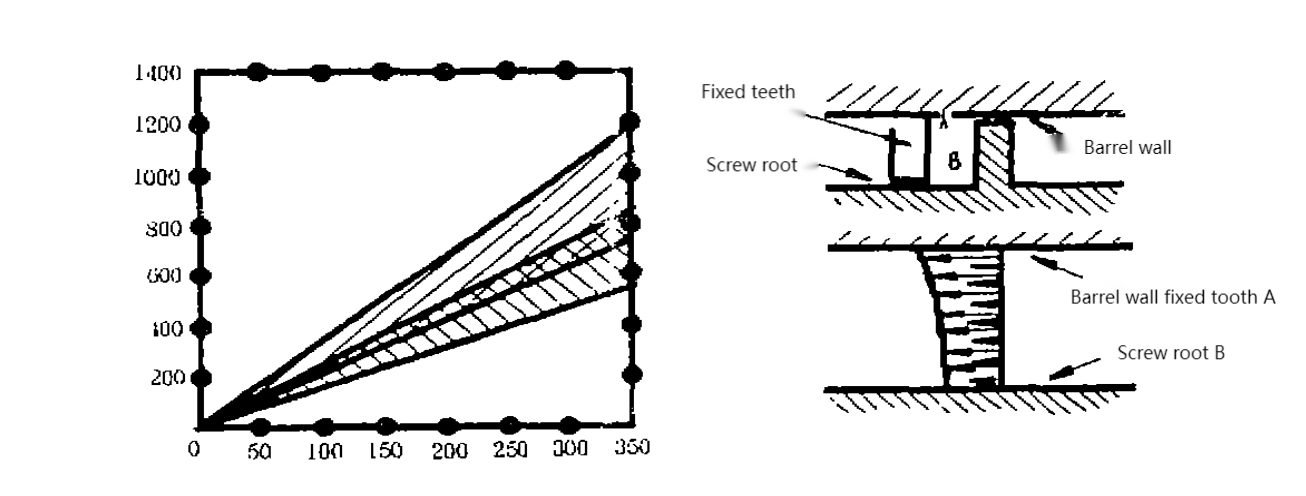
Figure 4: Relationship between stress and rotation speed
Figure 5: Stress distribution in the screw groove
Since the kneading element has interrupted threads, the pressure on the polymer is very small (see Figure 6 below). The presence of teeth affects the drag flow and pressure flow. The rotation and reciprocation of the screw causes each tooth to move in a certain trajectory relative to the screw (see Figure 2 above). The inner surface of the cylinder is swept by the screw elements, the material between the teeth and the interrupted threads is subjected to continuous and pulsating shearing, and the extrusion volume fluctuates in a sinusoidal wave. At a very small flow rate, the flow of the material is intermittent.
In short, the reciprocating single screw extruder can achieve excellent distribution mixing and dispersion mixing of the material at very low pressure, extremely short processing length, and residence time.
The function of teeth: The teeth in the screw groove, like a series of agitators, can redistribute the material multiple times by sweeping across the screw groove in a mixing motion: the teeth sweep across the interrupted threads so that the material cannot stay. The teeth can cause a certain axial backflow, eliminating the unevenness of axial temperature and components. The teeth provide some additional friction shear surface, which partially compensates for the reduction of friction shear surface caused by thread discontinuity.
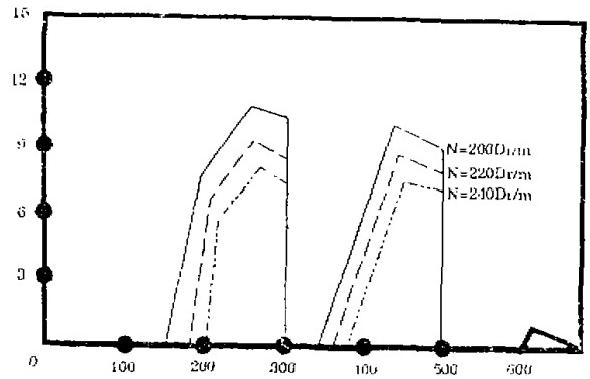
Figure 6: Distribution of pressure over screw length L when output and temperature are constant
6. Features:
Compared with ordinary extruders, under the condition of the same diameter, this machine has a smaller length-to-diameter ratio, and the machine structure is compact and sturdy. The torque is transmitted on a shorter screw, and the screw torque changes little. The mixing time of the material is short, and the time it stays in the barrel is correspondingly shortened. The shearing is uniform, the heating history is short, and the material is not easy to overheat and decompose. It is especially suitable for heat-sensitive plastics.
The screw extrusion pressure is low, or even no pressure is generated
The mixing and kneading performance is high, especially the axial mixing performance is good, and the orientation, cutting, folding, and re-orientation are suitable for highly filled materials.
The barrel is split and can be opened, easy to clean, and the color can be changed quickly.
A sensor is installed at the discharge port of the machine barrel, and the melt pump pressure can be adjusted or locked in time according to the requirements of the material.
In addition to the main feeding system, it is also equipped with a high-precision side feeding system to meet the processing requirements of various materials in various states such as powder, granular, and powder mixture.
In addition to measuring the temperature and pressure of the melt, the hollow teeth can also be used to add wet materials, paste-like viscous materials, colloids, melts, liquids, etc.
The price of the SJW-70 reciprocating single-screw extruder is only 1/5 of that of imported equipment.
7. Application:
This machine is mainly suitable for inorganic filling of various engineering plastics and general plastics (calcium carbonate, talcum powder, titanium dioxide, carbon black, etc.), rubber and plastic blending, plastic alloys, various masterbatches (anti-fog, degradation, weather resistance, cooling, rich color, etc.), various special modified materials (cars, ships, communications, home appliances, agricultural films, building materials, etc.), waste recycling and pharmaceuticals, food processing, etc. The main applications can be summarized as follows:
Different types of polymers can be blended to obtain new polymer alloy materials with specific uses.
Various mineral fillers (such as talcum powder, kaolin, and calcium carbonate) can be separately metered and added to the polymer melt, which can be easily made into filling materials with excellent performance and low price.
When preparing a concentrated masterbatch, good dispersibility can be obtained, greatly improving the production environment.
Various grades of glass fiber-reinforced and flame-retardant products can be produced. The glass fiber addition amount can reach 50%.
Efficient dyeing production can be carried out to effectively prevent color difference and color deviation.
Various specifications of cables and insulation materials can be produced.
References
- SJW-70 reciprocating single screw extruder Plastic Modification Newsletter 2000, Issue 2, P99
- Geng Xiaozheng The current status and development trend of continuous mixers for plastic modification Plastic Modification Newsletter 2000, Issue 2, P79
- Patent: Kong Xiangming Reciprocating Extruder China ZL 9922998291999
Get to know us through videos
Product Quality Index
Energy Generation