Application: Thermosetting materials such as phenolic molding plastics, Bakelite powder, unsaturated resin, and plastic sealing materials
Nation: Japan, China, Turkey, Mexico, Thailand, etc
Model: 3-flight Co-kneader and Clamshell barrel Twin Screw Extruder

From 2003 to 2019, a customer purchased a Co-kneader to produce thermosetting materials such as phenolic molding compounds, which changed the processing technology of the traditional open mill and greatly improved the stability of product performance. At the same time, a high degree of automation of Co-kneader improved the workshop production environment. The capacity per such compounding line can reach 3,000-10,000 tons/year. Xinda has become the largest supplier of thermosetting materials manufacturing equipment in China.
Customer’s Feedback and Review
1. With the unique mixing technology of low shear and high dispersion, the machine can accurately control the temperature of the material, and fully disperse and mix, with low friction heat. It can also control the temperature of the shaft and obtain the temperature of the solution when it produces heat-sensitive phenolic molding compounds, which can accurately control the material temperature. After full dispersion and mixing, the product has excellent performance and good homogeneity and stability.
2. The reciprocating and kneading machine(Co-kneader)and Clamshell Twin Screw Extruder has a high degree of automation in production. After the components such as phenolic resin, filler, auxiliary agent, and cross-linking agent are premixed, the closed feeding mode makes the production environment of the workshop clean and the working environment of the workers greatly improved, which significantly reduces the labor intensity of the workers.
3. Three-flight reciprocating machine or Clamshell twin screws has high productivity and low energy consumption, which can significantly reduce energy consumption compared with traditional open smelting production equipment.
4. The upper-stage reciprocating machine or twin screw extruder adopts a clamshell barrel design. When formulas change or the machine needs maintenance, it can be quickly opened and cleaned, which shortens the time of conversion and maintenance.


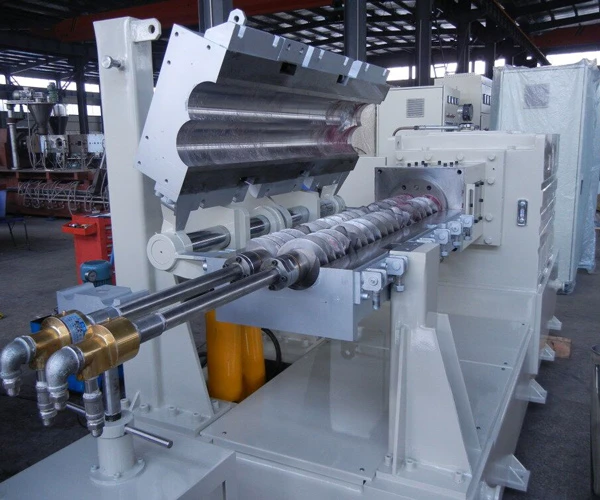
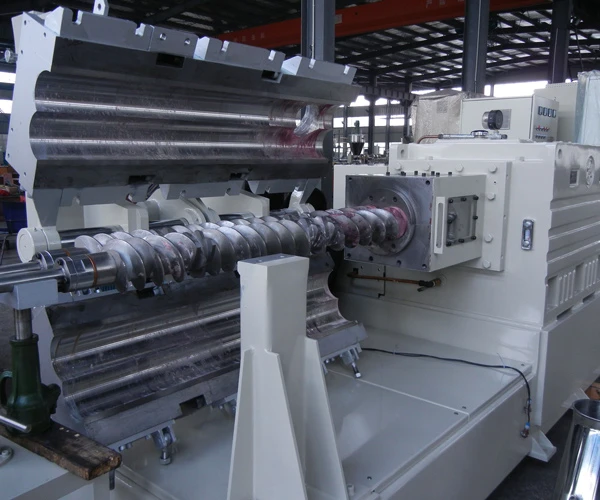